A Burning Question
When I last counted there were at least eight companies currently offering modulating/condensing boilers for residential/light commercial applications in the U.S. market. More offerings are waiting in the wings. In the last five years, this category of boilers has gone from virtually nonexistent (in North America) to being a significant sector of the market.

Most of these newer boilers have two operating modes: space heating and domestic water heating (DHW). These modes are mutually exclusive from the standpoint of temperature.
When the boiler operates in space-heating mode, its supply temperature is calculated based on the corresponding outdoor temperature (e.g., outdoor reset control). The warmer it gets outside, the lower the supply temperature from the boiler. Lower supply temperatures encourage flue gas condensation and boost thermal efficiency.

Since the boiler cannot produce both temperatures simultaneously, the DHW tank is typically treated as a priority load. Space heating is temporarily suspended during a call for domestic water heating. A typical piping diagram for this type of system is shown in Figure 1.
Although this concept works well in applications where the space heating system requires a single supply water temperature, there are times when multiple water temperatures are needed. An example would be when the boiler supplies panel radiators as well as slab-type radiant floor heating in the same home.
So how does a hydronic heating professional provide multiple water temperature with these boilers?
One approach that takes advantage of the controls already built into these boilers is called proportional reset control. It uses a manually set (nonthermostatic) mixing valve to provide the lower water temperature as illustrated in the schematic of Figure 2.
When the temperature of the “hot” stream entering a fixed-setting mixing device is reset, the temperature of the mixed stream leaving that device also tracks a reset line, one that's shallower than the boiler reset line (see Figure 3). This allows multiple fully reset supply temperatures to be created from a single boiler reset control.
In theory, you can create more than two fully reset water supply temperatures using proportional reset. One schematic for doing so is shown in Figure 4.
Before you conclude that proportional reset is the holy grail of hydronic temperature control, be advised there are limitations. A fixed-setting mixing valve is a “dumb” device. It cannot react to changes in water temperature or flow rate. Zone circuits turning on or variations in the heat source temperature easily create such changes. It's not a good idea to use proportional reset to supply a zoned distribution system, especially if that system operates with temperature setbacks or has high thermal mass. Such conditions can significantly lengthen the time it takes the distribution system to restabilize its supply temperature. The solution is simply to add a “brain” in the form of a motorized actuator for the mixing valve.
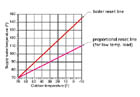
Don't Overcook The Water
The cardinal rule in applying condensing boilers is to operate them at the lowest possible temperature to achieve maximum condensation and highest efficiency. It doesn't make sense to operate a condensing boiler at a temperature higher than required by the load and then run this “overheated” water through a mixing device.Surprisingly, I've seen several installations that do this. Apparently the allure of the “high-performance” boiler was so compelling that the need to design the distribution system to harmonize with that boiler was overlooked. It's like buying a Ferrari racing engine and installing it in a farm tractor; the potential high performance will not be achieved.
Operating a condensing boiler at an inlet temperature of 160 degrees F yields a steady-state thermal efficiency in the range of 86 percent to 87 percent. Operating the same boiler with a return temperature of 90 degrees F yields a thermal efficiency of about 95 percent to 96 percent. That nominal 9 percent difference in efficiency is hard to overlook.
Seasonal efficiency gains will be even greater than the difference in steady-state efficiency. The more hours the boiler system operates at partial load conditions with reduced water temperature, the greater the fuel savings relative to a boiler with a fixed high-limit temperature that's based on design load conditions.

Surprisingly, I've seen several installations that do this. Apparently the allure of the “high-performance” boiler was so compelling that the need to design the distribution system to harmonize with that boiler was overlooked. It's like buying a Ferrari racing engine and installing it in a farm tractor; the potential high performance will not be achieved.
Operating a condensing boiler at an inlet temperature of 160 degrees F yields a steady-state thermal efficiency in the range of 86 percent to 87 percent. Operating the same boiler with a return temperature of 90 degrees F yields a thermal efficiency of about 95 percent to 96 percent. That nominal 9 percent difference in efficiency is hard to overlook.
Seasonal efficiency gains will be even greater than the difference in steady-state efficiency. The more hours the boiler system operates at partial load conditions with reduced water temperature, the greater the fuel savings relative to a boiler with a fixed high-limit temperature that's based on design load conditions.
Links
Looking for a reprint of this article?
From high-res PDFs to custom plaques, order your copy today!