Hydronics Workshop | John Siegenthaler
Combining a wood-fired boiler with a hydronic distribution system
Doing wood right

Image courtesy of mtreasure / iStock / Getty Images Plus.
Although they fluctuate continuously, the prices of all fossil fuels are inevitably trending upward as carbon reduction strategies continue to shape the energy markets. Government mandates aimed at phasing out fossil fuels in favor of electricity, and their associated consumer incentive programs, are steering many homeowners to electrically-driven heat pumps as their primary heating energy source.
I’ve written many PM columns discussing how air-to-water and geothermal water-to-water heat pumps can be combined with hydronic delivery systems to deliver efficiency AND superior comfort. This combination is a great solution for many consumers.
Not for everyone
Still, some rural homeowners have access to firewood and want to use it rather than fossil fuel or electricity as their primary heating energy source. Some harvest their own wood and view wood burning as a way of life.
The entry-level for home heating using firewood is to install a wood stove. Modern stoves using 2-stage combustion are significantly more efficient than that old cast iron stove in your grandfather’s hunting camp. But a wood stove cannot evenly heat all the rooms in a typical house. It can’t warm tile floors in a bathroom, allow room-by-room zoning or provide domestic water through a typical plumbing distribution system.
Wood burning technology has come a long way when compared to Grandpa’s camp stove. A modern wood-fired boiler properly matched to a hydronic distribution system can provide efficient combustion of a carbon-neutral fuel, whole house comfort, zoning and even domestic water heating. But details matter, and several of them are different from the “customary” details used for boiler selection, piping, control and operating techniques. Systems that don’t respect these specific details turn into expensive messes that can create dangerous conditions, annoy neighbors, and waste two-thirds of the energy in the wood.
If you live in rural America, where trees are abundant, you’ve probably seen some examples of poorly done wood-fired hydronic heating systems. Just follow the smoke trail on a cold winter morning. Chances are you end up at something like the installation shown in Figure 1.
FIGURE 1

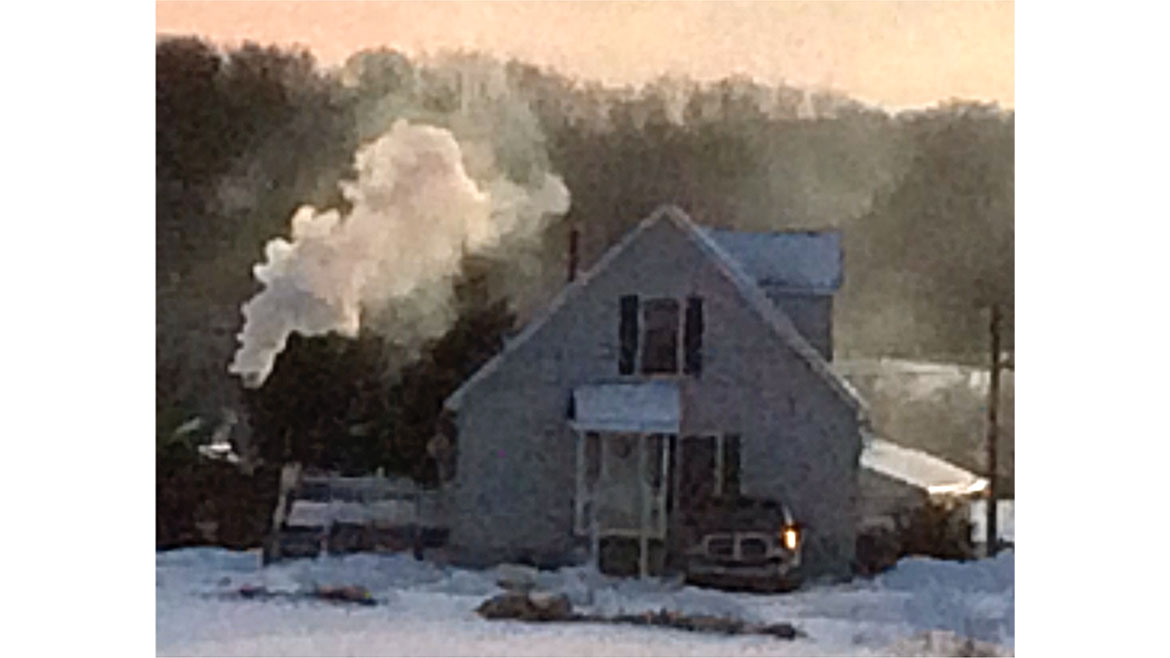
Many people, including plenty of heating professionals, have a preconceived image similar to Figure 1 when asked about wood-fired heating. They view it as dirty, smelly and dangerous. I can’t say that I blame them. For years, wood-fired hydronic heating in North America has been a “wild west” market where independently-minded individuals, especially those unfettered by codes and regulations, assemble “systems” that lack many of the details needed to convert cordwood into heat in a safe and efficiency manner.
Start with dry wood
When a living tree is felled, it can have moisture content upwards of 50%. This leads to a rhetorical question: Does water burn?
As obvious as that answer might be, some uninformed people do try to burn wood that was a living tree only a few days earlier.
Burning “wet” wood first requires the water it contains to be heated to its boiling point. Then the real physics kicks in. Changing liquid water at its boiling point temperature into vapor requires about 970 Btu/lb. The heat needed to do this has to come from the fire. That’s heat that will never help heat the building.
Figure 2 shows the tremendous effect of moisture content on the fuel value of wood.
FIGURE 2

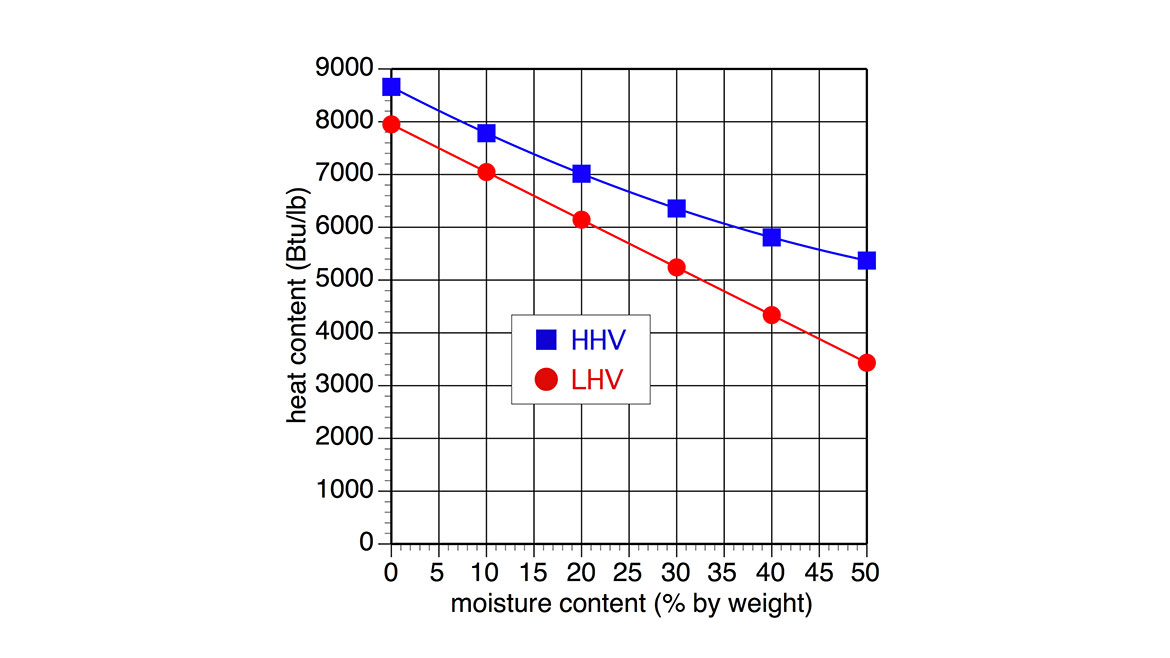
The upper (blue) curve shows the higher heating value (HHV) of wood on the basis of Btu/lb chemical energy content. The HHV assumes that all the water vapor produced during stoichiometric (perfect) combustion is recaptured, condensed back to a liquid, and that the recaptured latent heat is useful. The lower heating valve (LHV) assumes that the heat content of the water vapor produced during combustion is wasted.
Note that the graph doesn't distinguish between hardwood and softwood. On a Btu/lb basis, both have essentially the same chemical energy content. Hardwood has a higher density, so a given volume of hardwood — such as a face cord — has greater energy content compared to the same volume of softwood, assuming both have the same moisture content.
Both curves show a sharp decline in available energy as the moisture content increases.
The maximum suggested moisture content of firewood used in a cordwood gasification boiler is 20%. Anything lower is even better. Wood that’s allowed to dry for a nominal year, undercover, with free air circulation and elevated above-ground can typically achieve 20% or less moisture content.
Gasify it
The best way to squeeze heat from firewood is to burn it in a 2-stage combustion process. The first stage heats the wood above 300° F where it begins to give off pyrolytic gases. These are what produce the dancing flames over a wood fire. Every wood fire produces these gases, but the ability to unlock the chemical energy they contain varies considerably depending on the “container” in which the combustion occurs.
To extract as much heat as possible the pyrolytic gases need to be mixed, at a molecular level, with additional oxygen, and this mix needs to occur at a relatively high temperature. That’s where the second stage of a 2-stage process comes in.
After a fire is kindled, and a bed of coals has been established, cordwood gasification boilers use a blower to force the pyrolytic gases downward through a slot in a ceramic plate. Holes within that plate inject secondary air into the gases causing intense combustion, as seen in Figure 3.
FIGURE 3

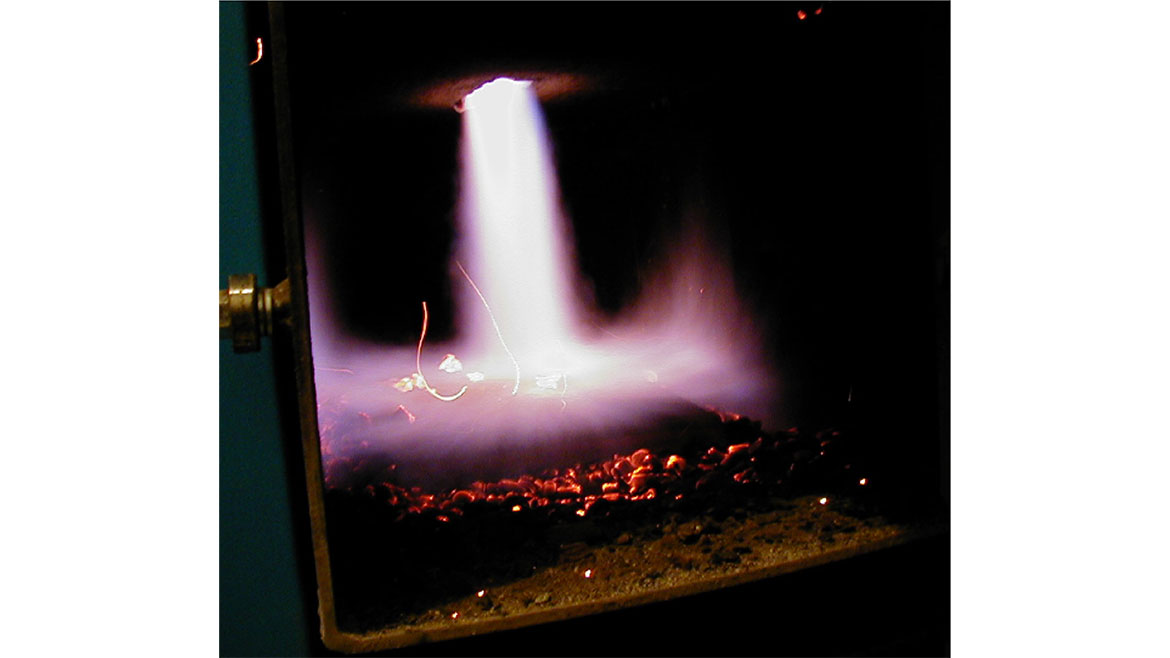
I’ve watched this process. It’s mesmerizing and could be described as a blow torch. It can generate temperatures over 2,000° F as the hydrocarbon molecules in the pyrolytic gas release their energy.
After the gases have combusted, the hot flue gas passes through the inside of several steel tubes where heat is transferred to the surrounding water.
When cordwood gasification boilers are operated correctly nearly all of the pyrolytic gases are burned. This greatly reduces the potential for creosote, which is a tar-like material that results from the condensing of uncombusted pyrolytic gases. Figure 4 shows an example of how creosote can coat the combustion chamber surfaces of outdoor wood-fired hydronic heaters.
FIGURE 4

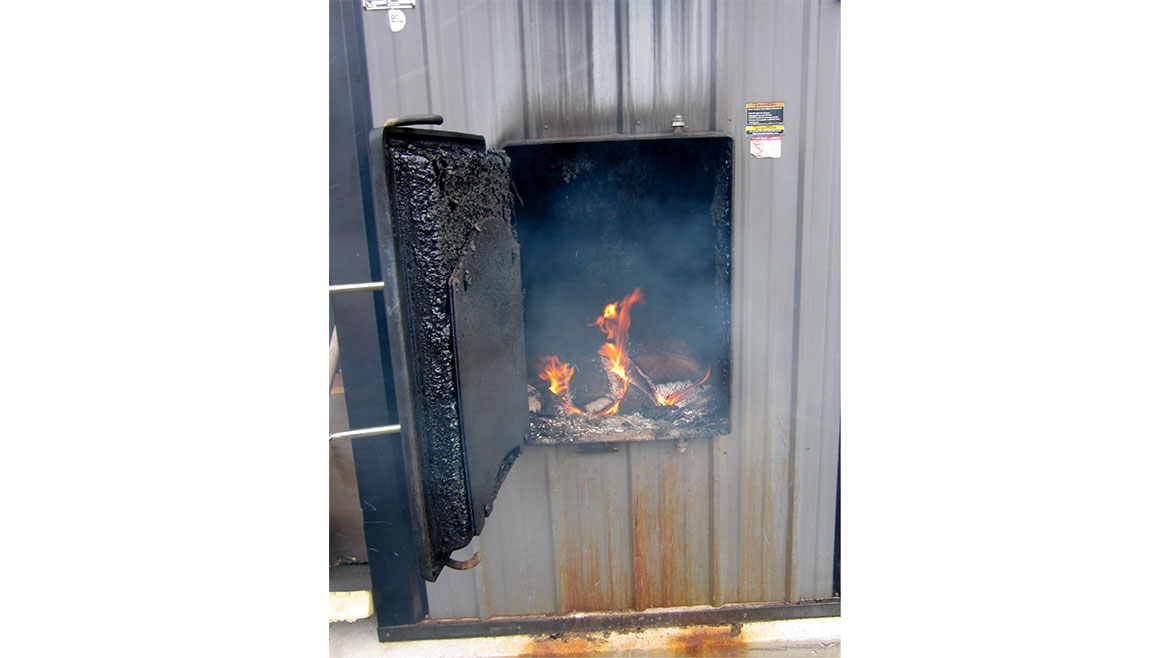
Given the right conditions, creosote will ignite and burn. One of the common places for this to happen is in a chimney where it has coated the inside of the flue passage. Once ignited in a tall vertical chimney, creosote can create intense jet-like fires that can destroy older masonry chimneys in minutes, and go on to burn down the building. Chimney fires are one of the “fears” that some people have regarding wood-fired heating. However, properly operated wood gasification boilers, burning dry wood and vented to Class A, UL-103HT insulated chimneys greatly reduce creosote formation.
Btu parking lot
Unlike wood stoves, gasification boilers should be operated as “batch burners.” Once a fire is started, the upper combustion chamber is fully loaded with wood, which is subsequently burned as hot and fast as possible. The resulting rate of heat output is often much higher than the current heating load of the building.
The solution to this mismatch is not to throttle back the combustion, but rather to park the heat output beyond that needed in the building in a thermal storage tank. The volume of the tank can be calculated using Formula 1.
Formula 1:
Where:
v = required thermal storage tank volume (gallons);
w = weight of firewood that can be loaded in the combustion chamber (lb);
n = average efficiency of the combustion process (decimal percent);
∆T = temperature rise of the tank based on absorbing all heat from the combustion (°F); and
701 = a constant based on the heating fuel value associated with 20% moisture content firewood.
For example, consider a cordwood gasification boiler with a combustion chamber that, when fully loaded, can hold 65 pounds of seasoned firewood. Assume the boiler’s average combustion efficiency is 70%. Determine the size of the thermal storage tank assuming the water in the tank will rise 60° F as it absorbs heat from burning the full charge of wood, and that there is no heating load in the building when this takes place.
It’s doubtful that a designer could find a readily available tank with a volume of 531 gallons. Instead, they might specify a 500 or perhaps 600 gallon tank. In either case, it’s a big tank.
Most mechanical codes require any tank, with a volume over 119 gallons, and the potential to operate under pressure, to be listed under the ASME Section VIII pressure vessel code. These tanks are available, but they are not cheap, light, or likely to fit through a typical 36” exterior door. They should be insulated to a minimum of R-28 °F•hr•ft2/Btu, typically using closed-cell spray polyurethane foam that is rated for at least 200° F.
A fully insulated storage tank of this size and construction is a big investment, but it’s essential to the proper operating of a wood gasification boiler. I’ve seen systems with wood gasification boilers where no storage was provided, and the results were not encouraging. The water temperature climbs quickly as the wood is incinerated at rates much higher than the heating load. The upper temperature limit of the boiler’s controller is met within a few minutes and the combustion fan shuts off. What would otherwise be a “high tech” method of extracting energy from wood turns into an oxygen-starved, simmering, smoky mess (revisit Figure 1). Do it right, or don’t do it at all.
More to come
So far the takeaways are: 1) Use a cordwood gasification boiler to burn “batches” of properly seasoned firewood, as hot and fast as possible; and 2) properly sized thermal storage is essential in maximizing the performance of these boilers.
In part two, we take a look at piping and control concepts. You’ll see how all the details come together.
Looking for a reprint of this article?
From high-res PDFs to custom plaques, order your copy today!