The Glitch + The Fix: High-end DHW issues

The Glitch:
The system shown in Figure 1 was installed to provide domestic hot water to a high end house with several bathrooms. The installer selected the largest 119 gallon indirect water heater available from his supplier. The tank’s internal heat exchanger was rated to transfer 250,000 Btu/h when supplied with 180° F water from the boiler. He piped it in with 1 inch copper tubing, because that was the size of the piping connections on the tank. He used three identical zone circulators, one for each boiler, and one for the indirect tank. He used a larger circulator for flow to the space heating portion of the system.
Being concerned about a potential complaint over not enough hot water, he convinced the owner to double up on boiler capacity, and thus installed two boilers, each rated at 250,000 Btu/h. He also set the internal high temperature limits on each boiler for 200° F during a call for domestic water heating (because that’s as high as the control would go). He assumed that 200° F water through the coil will significantly increase the heat transfer through the tank’s coil heat exchanger.
When put in operation, the system experienced serious problems. The 15 gpm shower in the master bathroom only remained comfortable for about five minutes, followed by a rapid drop in water temperature. The boilers also short cycle and emit “knocking” sounds during the domestic water heating mode. Even worse, the house quickly overheats each time there was a call for domestic water heating.
Can you spot at least five details that are incorrect, and recommend how to fix this situation?

The Fix:
Doubling the boiler heat output, and setting the boiler limit to 200° F will produce slightly better heat transfer in the storage tank (relative to the rated heat transfer based on 180° F water from the boiler). My calculations show the increase to be about 25% assuming a cold water inlet temperature of 50° F, and a hot water delivery temperature of 120° F. Under these conditions, the indirect heater was capable of transferring about 312,000 Btu/h to the domestic hot water. This is still far short of the full boiler capacity of 500,000 Btu/h. This system is “bottlenecked” by the performance of the internal coil heat exchanger. The remedy is to select an indirect tank with an internal heat exchanger that can transfer the full 500,000 Btu/h output of the boiler system, or use an external brazed plate heat exchanger that can do the same.
There is also no means of hydraulic separation between the boiler circulators and the circulator supplying the indirect tank, or the space heating circuit. This puts the boiler circulators in series with the other circulators. This piping, combined with the lack of a check valve, also allows hot water to flow backwards through the space heating distribution system whenever there’s a call for domestic water heating, but no call for space heating.
Other errors include:
- The 1-inch piping and zone circulator supplying the indirect tank will not provide sufficient flow to convey 312,000 Btu/h (much less 500,000 Btu/h) to the coil. Assuming a nominal 20° F temperature drop across the coil, the flow needs to be about 50 gpm. That’s a lot more than a typical zone circulator can provide, and certainly more than a 1-inch pipe should be carrying. That flow requires a minimum 2-inch pipe. An indirect tank that was rated for 500,000 Btu/h input would come with larger piping connections - mostly likely 2-inch;
- The placement of the boiler supply temperature sensor is incorrect. As shown, it would only sense the temperature of the boiler on the right side;
- When low-mass boilers are used, the associated boiler circulators should push flow into the boilers. This keeps the pressure inside the boiler elevated, and thus widens the margin against steam flash or circulator cavitation. This is especially important when the boiler water will be in the range of 200° F during a call for domestic water heating;
- The check valves on the boiler inlet piping are much too close to the underlying tees. This is likely to produce rattling sounds. There should always be a minimum of 12 diameters of straight piping on the inlet side of any check valve to smoothen out turbulence caused by upstream devices;
- There is no central air separator in the system; and
- There is no point of distribution ASSE 1017 rated thermostatic mixing valve on the domestic hot water delivery piping. That sets up a very dangerous situation is someone happens to set the controller for the domestic water portion of the system to a high setpoint in an attempt to provide longer showers.
Figure 2 shows how all these glitches can be fixed.
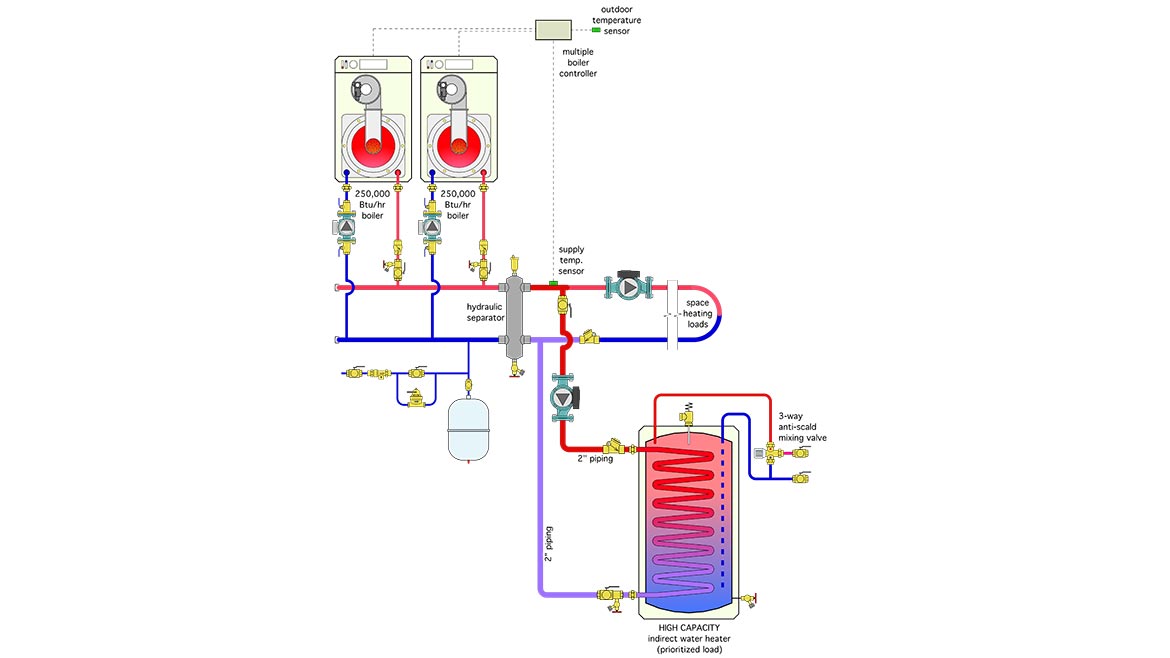
Looking for a reprint of this article?
From high-res PDFs to custom plaques, order your copy today!