The Glitch & The Fix: Circulator problems

The Glitch:
The piping shown in Figure 1 is a partial representation of an actual installation. The portion of the system shown on the right side supplies 14 independently controlled zones, with 14 circulators each having a nominal 200-watt power input. There’s another circulator (P1) piped in above the zone circulators. There’s also a crossover pipe between the supply and return sides of this piping assembly. The occupants of the large home where this system is installed state that when only 2 or 3 zones are operating, comfort is fine. However, as more zone circulators turn on, there’s less and less heat output from all the active zones. Can you diagnose why this is happening, and suggest alternate methods for constructing this portion of the system?
Figure 1

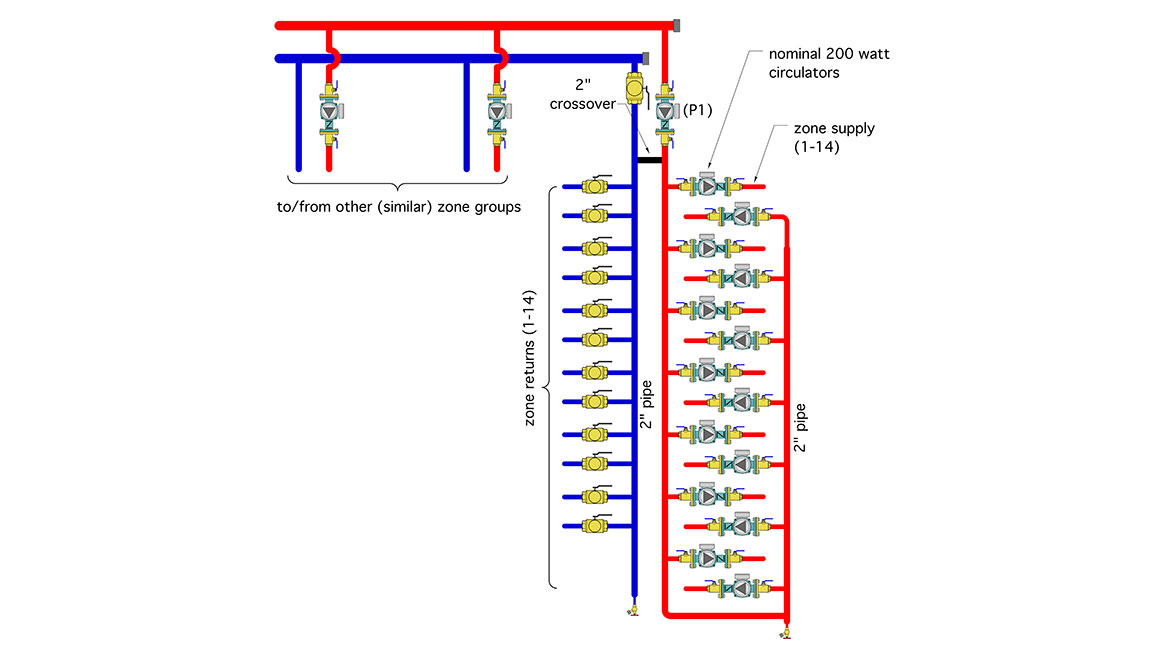
The Issues:
If all the circulators are operating, which should be assumed as possible under design load conditions, the electrical power demand is cringe-worthy (14 zone circulator x 200 watts = 2,800 watts = 2.8 KW = 9,560 Btu/h). Furthermore, that power demand is only about half of the total possible demand of the system based on how the other zone groups are constructed. Think about it, on a mild day in spring or fall, just turn off the boilers, turn on all the circulators, and let fluid friction heat the house. Surely we can do better in terms of power input to distribute heat — even in large houses.
I would also question if 2” copper piping for the vertical headers is sufficient for the anticipated flow rates if most, or all, circulators were operating. Granted, that condition would not occur often, but when it did, the flow velocity in the left side vertical supply header could be high enough to cause a significant loss of hydraulic separation between the circulators, which would lead to significant flow rate variation in the zones. The greater the number of active zones, the greater this variation.
It’s also likely that the total zone flow rate will be higher than the flow rate through circulator (P1). This causes some of the flow returning from the zones to pass through the bypass pipe and mix with the hot water supplied through circulator (P1). This mixing lowers the temperature to the zone circulators, and is likely the cause of the reduced heat output as more zone circulators are operating.
Other issues include a lack of purging valves on the return side of each zone circuit, and circulator inlets placed very close (e.g., less than 10 pipe diameters) from header tees.
The Fixes
One alternate configuration is shown in Figure 2.
Figure 2

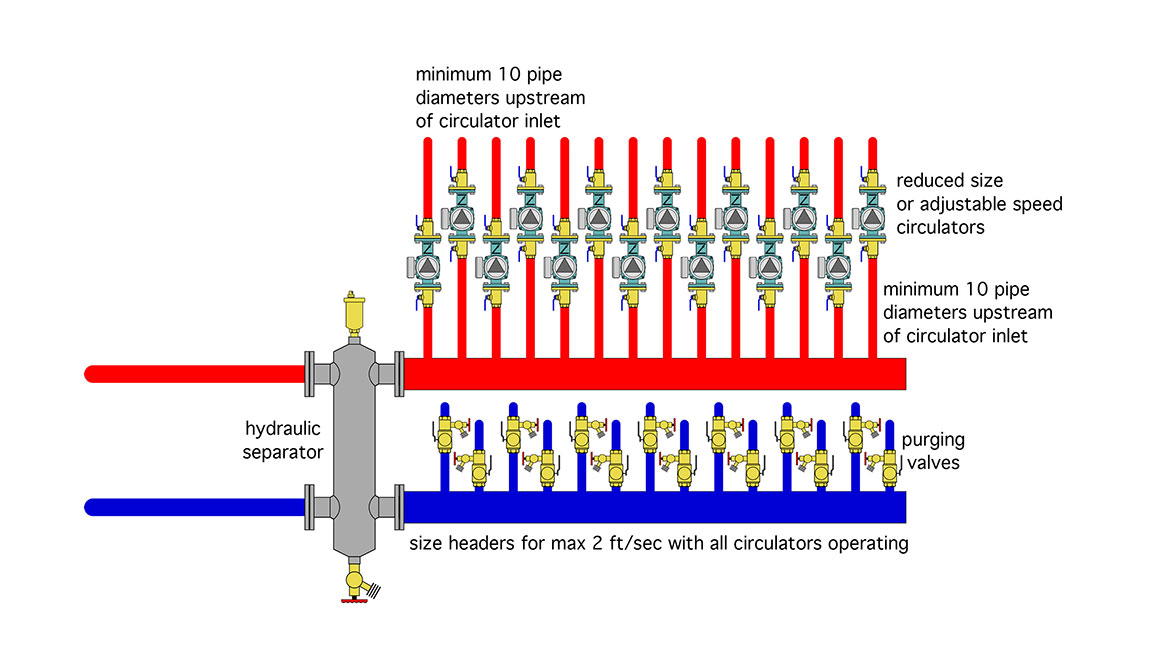
This alternative stays with zone circulators, but assumes downsizing those circulators, or using speed-adjustable circulators, to reduce power consumption.
A hydraulic separator is used in combination with upsized supply and return headers. The separator isolates the flow dynamics of the zones from that of the circulator creating flow to this subassembly. The generously sized header “reinforces” the concept of low-pressure drop in the common piping — the fundamental concept behind hydraulic separation.
Figure 3 shows another alternative based on a single variable speed circulator and zone valves.
Figure 3

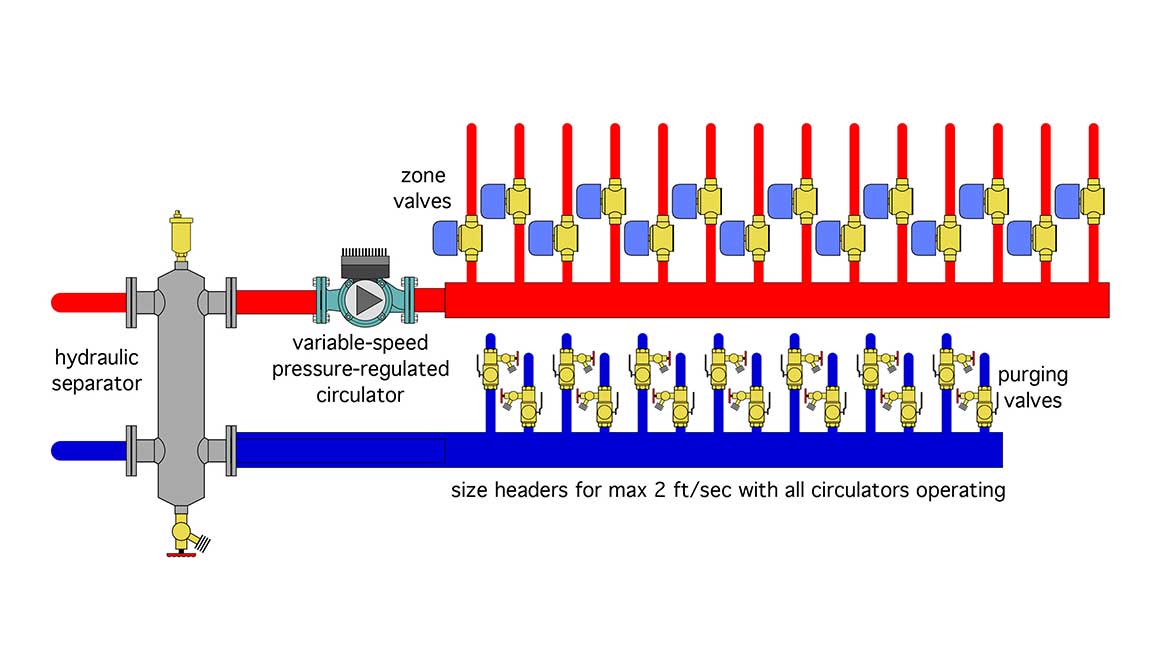
The hydraulic separator again isolates the flow dynamics of the 14 zone circuits from those created in other portions of the system. It allows the variable speed circulator to operate over a wide speed range without interference.
The piping between the hydraulic separator and headers should be as large as possible to minimize pressure drop. It’s OK to go back up in pipe size after the circulator to keep the flow velocity in the main header no higher than 2 feet per second.
Another possibility
I’ve not seen the final details used in this system. Given what is known, there’s a possibility that circulator (P1) in Figure 1 was intended to be a variable speed injection circulator. Its speed at any time would determine the flow rate of hot boiler injected into the header below and thus the reduced supply water temperature to the 14 zones. Assuming this was the intent, either of the two piping configurations shown in Figure 4 would provide better hydraulic separation between the injection circulator and distribution circulator.
Figure 4

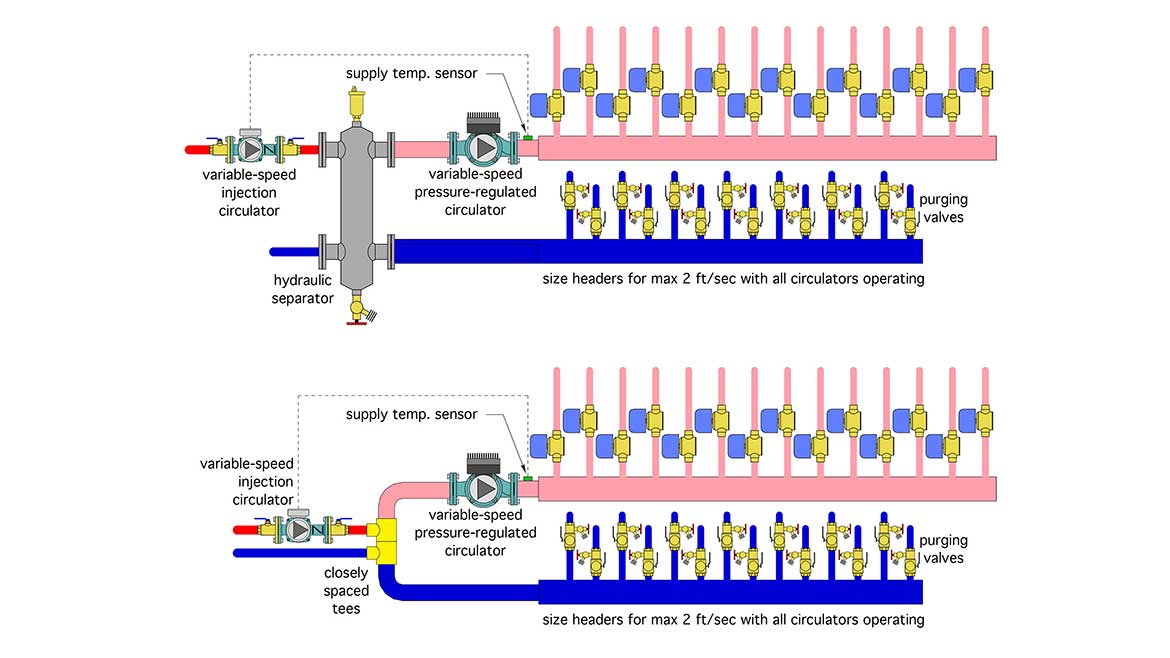
Looking for a reprint of this article?
From high-res PDFs to custom plaques, order your copy today!