Maximizing efficiency and economics on small-diameter piping projects
Preferences for piping materials have evolved, and joining solutions need to keep pace.

Victaulic's QuickVic SD Installation-Ready System is an innovative plain end pipe joining technology designed for use on small-diameter carbon steel piping systems that enables material savings and efficiency gains to boos commercial and industrial projects.
Piping material is a top consideration for every commercial HVAC construction project. Since the choice of piping material impacts project efficiency and economics, it is important to factor in material costs, as well as the expenses associated with installation and maintenance when determining the best solution. This becomes especially critical for what typically is the largest segment of HVAC systems: Small-diameter piping.
WEIGHING THE OPTIONS
For years, copper tubing has been a top choice for piping systems up to 2.5 inches in diameter, but recently, carbon steel pipe has gained ground. Part of the reason for this change is cost. Copper tubing can be as much as 60% more expensive than carbon steel pipe for small diameter HVAC jobs.
Considering material selection alone, it is apparent that carbon steel pipe is the more cost-effective option, providing many of the same benefits of copper tubing at a lower price point. But while carbon steel pipe is less expensive, the cost of its installation is higher.
When small diameter copper tubing is installed, two types of joining methods are used. One option is to sweat the joint, which introduces fire to the project site and the associated hazard risks, along with the added safety requirement of a fire watch. In addition to greater risk, this method is time consuming and labor intensive. If mistakes are made or tubing needs to be replaced, the cost of cutting out the section and installing new tubing can be substantial. The second option, pressing, is faster than sweating, but it requires expensive fittings and special installation tools. And when pressed tubing needs to be replaced, the time and cost investment rivals that of replacing a sweated joint.
Joining carbon steel pipe brings similar challenges. Pressing is faster and cleaner than threading, but it brings with it installation disadvantages similar to copper press. Threading eliminates these shortcomings, but is more time consuming and requires bulky equipment that introduces clutter and added mess to the jobsite.
Irrespective of the joining method used, inspecting for system integrity poses challenges. Of all the traditional joining methods, there are few that can be easily inspected visually to confirm proper installation before testing the system. Formal system testing takes time, and when irregularities are identified, corrections add even more delays to the project schedule. The effectiveness of the testing is also a concern. In some cases, field testing does not detect faulty joints that eventually experience failure when taxed by operating conditions. When repair or replacement is required, the system must be taken out of service, which carries its own costs.
With limited joining options, companies are forced to choose between solutions that are less than ideal – using expensive copper tubing or less costly carbon steel pipe that takes longer, requires more equipment on the worksite and is messier to install.
A more efficient solution would allow small diameter carbon steel pipe to be installed with a faster joining method.
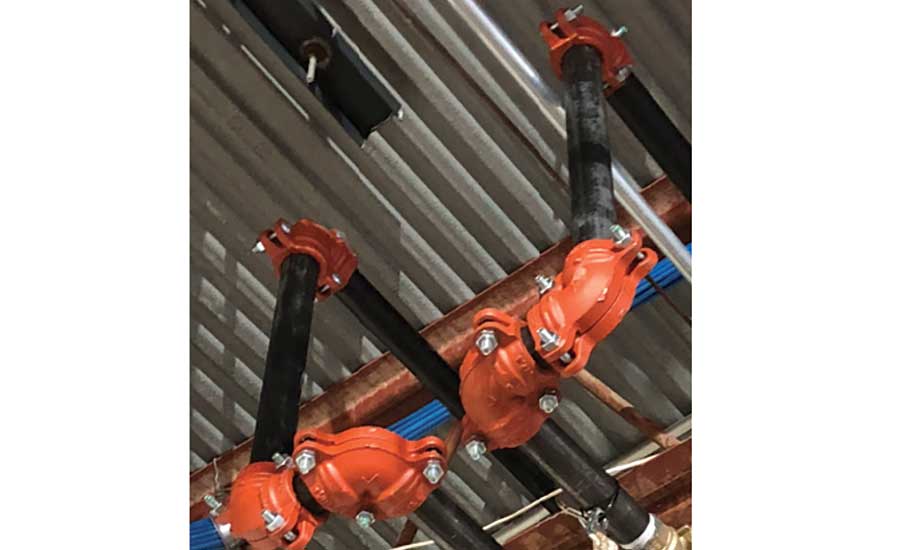
Victaulic's plain end pipe joining solution is simple to maintain, the company notes. The joints can be disassembled and reinstalled without the need to cut out, remove and replace piping.
TAKING THE NEXT STEP
The introduction of an innovative and durable plain end mechanical joining solution that can be used with carbon steel pipe has the potential to change the status quo, delivering the speed of installation normally associated with copper systems and reducing total installed cost. It is a robust coupling that is simple to install, visually verifiable and allows disassembly without damaging the pipe or joint. In addition to these installation advantages, because this connector is repositionable and reusable, it also reduces material and labor waste.
Time-savings hinges on simplified installation. Plain end mechanical couplings are manufactured and shipped so they arrive on site ready to install. No disassembly is required, and there are no loose parts. A one-piece integral gasket is part of the coupling and requires no wetting, a feature that not only expedites installation, but also eliminates internal corrosion. And unlike other joining methods, plain end mechanical joints can be installed by hand or with a battery-powered tool, in some conditions as much as four times faster than alternative methods.
Making sure the joint is properly made up is also simpler with the plain end joining solution, which allows the connection to be verified visually after installation. This unique gasket is designed not to seal until the coupling is mechanically secured on the pipe, a feature that allows the joint to leak during an initial system test if the coupling has not been assembled properly. If leakage occurs during that test, the system can be depressurized and drained completely so any mis-assembly can be corrected.
It is easy for installers to know when the coupling has been installed correctly. When the bolt pads come into contact with no visible daylight between them, the joint is properly seated. A retainer inspection window and knurled insertion depth markings on each piece of pipe also help ensure correct assembly throughout the installation process. Once installed, plain end mechanical joints are immediately ready for full service.
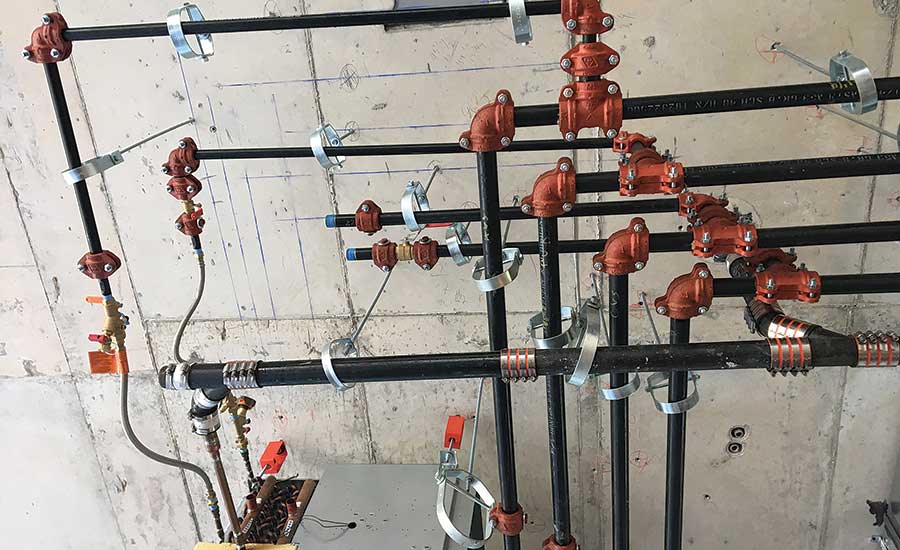
The QuickVic SD products are simple to install, visually verifiable and sllows disassembly without damaging the pipe or joint. Because the connector is repositionable and reusable, it also reduces material and labor waste.
These joints also are simple to maintain. They can be disassembled and reinstalled without the need to cut out, remove and replace piping.
ANSWERING INDUSTRY NEEDS
Preferences for piping materials have evolved, and joining solutions need to keep pace. The design of the plain end coupling is evidence that targeted development efforts can produce components the industry needs, introducing an efficient solution that drives down costs and delivers consistent, reliable performance.
Looking for a reprint of this article?
From high-res PDFs to custom plaques, order your copy today!