PM Profile
Mechanical contractors need to embrace new technology or get left behind

Images courtesy of Autodesk and The Brandt Companies
In today's rapidly evolving world, the construction industry is undergoing a profound transformation, driven by technological advancements that are reshaping the way projects are planned, managed, and executed. Mechanical contractors, who play a pivotal role in the construction process, are not exempt from these changes. In fact, embracing new software technology is becoming increasingly essential for their success and competitiveness.
Out of more than 2,500 industry leaders across architecture, engineering and construction (AEC) surveyed in Autodesk’s 2023 State of Design & Make Report, 79% of respondents said the future growth of their companies will depend on digital tools.
Plumbing & Mechanical Chief Editor Nicole Krawcke had the chance to chat with Chad Salge, vice president of virtual design and engineering at The Brandt Companies, a Carrollton, Texas-based mechanical contracting firm, about its digital transformation journey.
PM: Can you give us a little background information on The Brandt Companies? How long has the company been in business and what services does it offer?
CS: Brandt is a leading mechanical, electrical, and plumbing firm in the United States. In 2022, Brandt was acquired by Southland Industries. This acquisition united a team of more than 5,000 talented individuals across 35 states with full lifecycle expertise from engineering through fabrication and installation to post-construction services, including operations, maintenance and energy services. Our combined entity works on some of the most complex projects in the U.S.
PM: How did you get your start in the industry, and how did you end up at Brandt?
CS: After graduating from Texas A&M University in 2005 with an electrical engineering degree, I stumbled into the industry through a family connection to Lockwood Greene, which had been purchased by CH2M Hill when I joined. I began my career performing detailed electrical design tasks and later moved into project engineering and project management. At CH2M, I was exposed to every discipline and vertical market, including global, full service architectural, engineering and construction services. After over 12 years at CH2M, a neighbor presented me with the opportunity to come to Brandt. After seeing Brandt's caliber of services and people, I enthusiastically joined the team.
PM: Brandt was acquired by Southland Industries last year — what lessons have you learned from that acquisition and how has it positioned the company for success?
CS: When I heard the news of Southland acquiring Brandt, I was well prepared for it due to my prior experience. In my opinion, the biggest lesson to learn from an acquisition is to remain people-focused throughout the entire process. Cultural alignment between Brandt and Southland was well-vetted during the due diligence process, and it has proven to be very beneficial as we develop and execute the integration plan. Both organizations have a healthy common respect for what each one brings to the table, and that has led to efficient and thoughtful progress as we continue to plan alignment within the greater organization. We have a sign in front of our offices that says, ‘People are our greatest asset,’ and I am thankful that we have stayed committed to that philosophy.
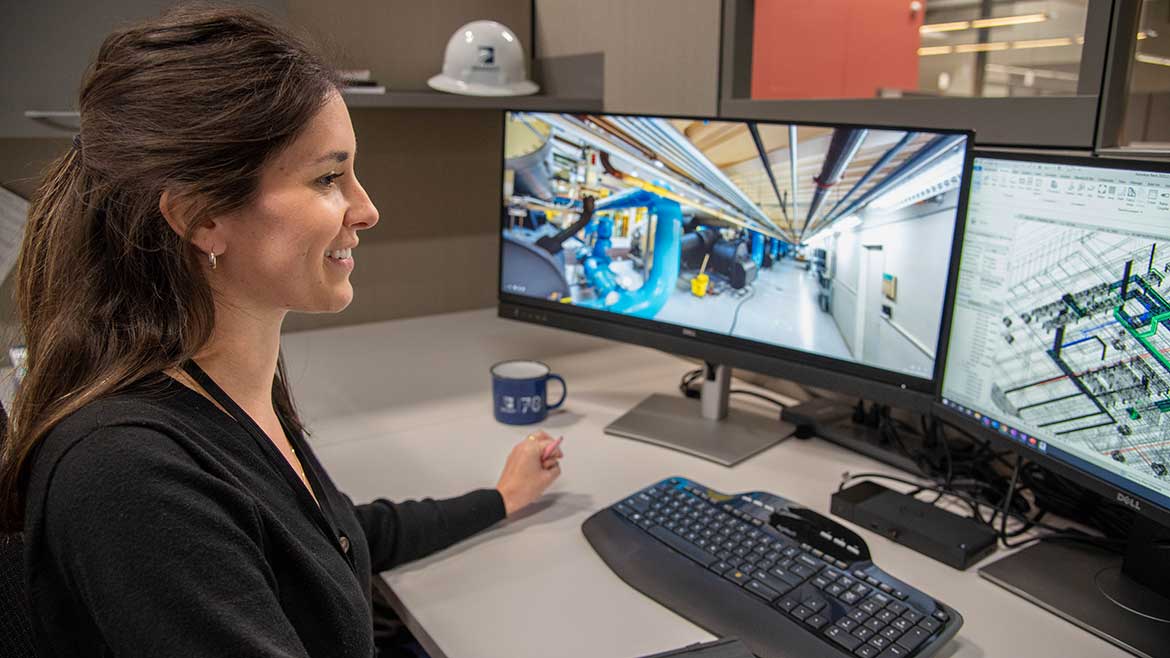
PM: How has the acquisition impacted how Brandt uses technology? Why did you decide to migrate and standardize on Autodesk Build?
CS: Innovation is at the core of Southland and Brandt — and our combined team is committed to implementing technologies that increase productivity and reduce risk. We invest in resources that ensure we are properly investigating and leveraging beneficial technologies available today. As a result, there has been a lot of complementary value in having our groups that are focused on innovation come together. Early on, Brandt capitalized on the Virtual Desktop Infrastructure (VDI) platform that Southland implemented a few years ago, further aligning our integrated efforts.
Another example of how we’ve implemented software to increase productivity and reduce our risk is Brandt’s migration to Autodesk Build as a construction management solution. The platform we were previously using did not allow access to design models within a single platform, which caused additional steps in the workflow for our design-build projects, so we formed a task force to evaluate the construction management offerings available in the marketplace. Through a very focused mission and thorough investigation, we chose Autodesk Build due to the ability to work in a single source application throughout a project's entire lifecycle, the platform's mobility and access, and the interface's intuitive nature.
PM: How has that migration helped Brandt overall?
CS: Through a very swift ramp-up process and support from all aspects of the business, we have effectively and quickly migrated to Autodesk Build. The platform has brought resources and insights to a broader group of people. Due to Autodesk Build’s mobility and access, the field foreman and superintendents can now more easily access all information on a project. The previous platform we were using was not cloud-based, so there was a process in downloading and getting to the project information that created a barrier in access. Specifically regarding access, Autodesk Platform Services Viewer has helped bring modeling insight and further context for our entire project team. Instead of needing Revit or Navisworks on their respective machines, all Brandt users can now navigate the model from any machine, anywhere. That level of access has and will continue to have big implications on our efficiencies and workflows. We also have utilized the Insights module to bring our reality capture services to the project site within Build. Forms and Meeting Minutes are also modules utilized by our teams. The ability to access that information in one platform and interconnect information within the platform (linking to RFIs, submittals, issues, etc.) has been very beneficial.
PM: How is technology helping to create more efficiencies within the company?
CS: Technology allows for greater and more seamless access. As a result, there are a lot of efficiencies in how our employees navigate the enormous amounts of data associated with a design and construction project. From abilities like slicing and dicing data in a meaningful way, visualization tools, artificial intelligence built into software platforms, and many more aspects, technology has allowed users to get to data more efficiently than ever before. For instance, a project superintendent can easily access a model to understand how a system communicates with architectural features, the impact on other utilities in the area, the scheduled completion date, and the cost associated with performing the work. The level and ease of access to information provided by technology reduces the need and associated risks in going to several sources to collate the data.
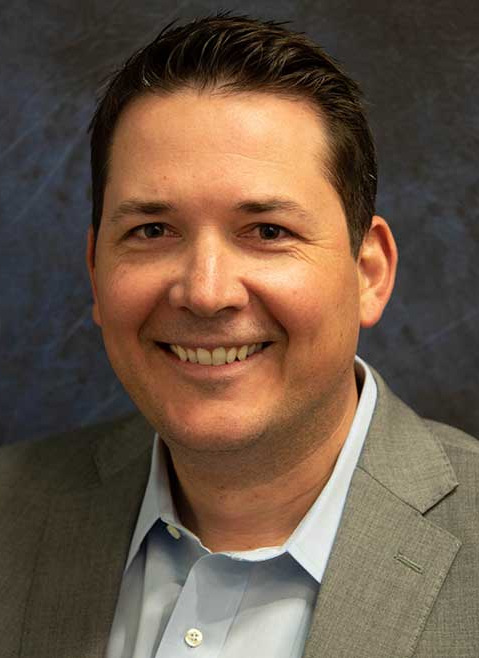
Chad Salge, vice president of virtual design and engineering at The Brandt Companies.
PM: Is it important for mechanical contractors to embrace new technologies? Why or why not?
CS: It is very important for mechanical contractors to embrace new technologies. Over the last several years, there has been a major confluence of construction and technology that has changed the way we currently look at how we conduct our business as an MEP subcontractor and design-builder. Our workflows have changed pretty dramatically over the last 10 years due to the availability and progression of technological platforms. That wave of tech influence is only getting bigger, and the technology-focused undertow is drawing the construction industry closer and closer to that wave. I think any viable business would rather be on top of that wave and coast into the destination as opposed to being tossed around and spit out once it breaks.
PM: Will AI technology impact the MEP software market? Why or why not?
CS: The industry is already embracing AI. Over the last few years, significant breakthroughs have made the technology even more applicable to the MEP industry. Chat GPT, generative design within 3D modeling platforms, data analysis, and AI have immense applications and implications in the MEP industry. If you look at the different steps in the project lifecycle and software that has already been developed for each step, you can envision a future where you use ChatGPT to begin to lay out the framework for a project, utilize that information to feed into a generative design platform to lay out the components of a project in a cloud-based model, leverage that model to automatically spool the different systems, use those spools to automatically procure material, prefabricate the spools and construct the project, use reality capture for automatic progress tracking and finally leverage building data analytics to manage and service the building moving forward. As a result, many software companies are focused on developing AI products for the MEP industry. Specifically, we have decided to embrace AI to further enhance and advance our capabilities to develop standard operating procedures and gain better insights on construction progress tracking.
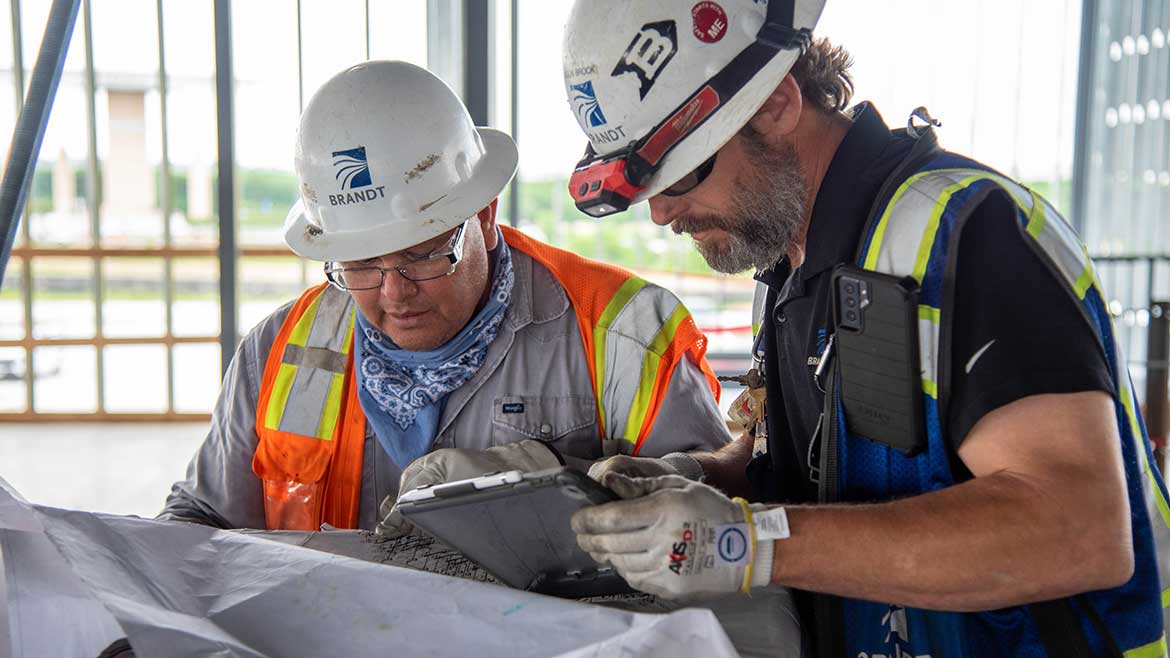
PM: Anything else you want to add?
CS: As we move forward together as one company, we are joining our technology and innovation teams together to push the company and the industry forward. With all the technological advancements and the leveling of software capabilities, there is a big need to leverage the insights of skilled tradespeople that our company employs and represents. Critical thinking and possessing true construction experience will continue to be paramount to effectively constructing resilient buildings in the future. Autodesk has committed to building out more capabilities specific to that invaluable insight from our tradespeople and we are partnering very closely with them to help drive platform improvements in these areas. It is very impressive to see where we have come in our industry, and we are grateful that Autodesk has embraced and invested so much in that advancement.
Looking for a reprint of this article?
From high-res PDFs to custom plaques, order your copy today!