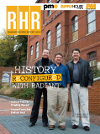
Chris Morrison, Steve Kay and Dan Foley at the Wormley School condo building. Photo credits: Uponor
A team of construction industry professionals with a track record of successful projects recently transformed a 125-year-old school building in the nation’s capital into seven condos priced around $1 million. Radiant floor heating is a key component of the building’s new comfort system.
“Our charge from the builder was to deliver a best-of-the-best heating and cooling system to meet its vision for the project,” saysDan Foley, president of Foley Mechanical in Alexandria, Va. “We weren’t just the radiant guys; we were the comfort guys. We did the ventilation, not just make the floors warm.”
Located in the heart of Washington’s busy Georgetown neighborhood, Wormley School is listed on the National Register of Historic Places. Built in 1885, the school was named for James Wormley (1819–1884), “a nationally renowned Washington entrepreneur who was a passionate advocate for the education of the city’s African-American children,” according to the Wormley website (www.wormleyrow.com).
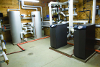
The Wormley boiler room features two Lochinvar Knight condensing gas boilers, two Heat Transfer Products Super-Stor commercial indirect water heaters, Taco controls, Grundfos pumps, a Caleffi Hydro-Separator, and tekmar staging and snow-melt controls.
“Parking in Georgetown is always a nightmare,” says Foley, a former president of the Radiant Panel Association and current RPA board member. “Our work was limited by the architectural commission. The building had to look the same from the outside when we were done. For example, it had to have single-pane glazing, which affected our heat-load calculations.”
Nevertheless, builder and developer Encore Development, contractor Foley Mechanical and architect Cunningham|Quill overcame these and other challenges to transform the vacant and dilapidated school building into Wormley Row, a desirable property in the nation’s capitol. Encore Development ownersSteve KayandGary Kirsteininvolved Foley while plans for the project were still in the early stages.
“Bringing all the players together early in the process saved a lot of potential headaches down the road,” Foley says. “Multiple meetings between the architect, builder, engineer and our staff resulted in a system designed to provide all the modern amenities in a historic building.”

Dan Foley (left) and Ron Etter of Foley Mechanical in the mechanical room of the newly renovated Wormley School building.
Radiant Rehab
The state-of-the-art radiant floor heating system consists of more than 15,000 feet of PEX tubing that Foley Mechanical’s crew installed in two days to accommodate the demanding work schedule. The building’s ceiling heights of 9 to 14 feet and window heights of 6 to 8 feet led the construction team to choose radiant floor heating, Foley says.While radiant heat provides interior comfort, a snow-melt system - also installed with PEX tubing manufactured by Uponor - provides safe access on the outside parking ramp and public walkways.
Foley worked closely with Summit Engineering on system design. The interior of the building was completely gutted, which gave Summit and Foley Mechanical a greater degree of freedom in designing the radiant system, Foley says.
A radiant heating expert with more than 15 years’ experience, Foley Mechanical has developed a preferred method for installing its jobs, including the types of controls and PEX piping configurations. Wormley Row was Summit’s first radiant heating project.
“We worked as a team, rather than fall into the more typical adversarial relationship that can exist between the engineer and contractor,” Foley says. “I’m not an engineer; I can’t stamp plans. But our office brings a lot of practical knowledge to the table.”
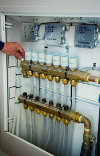
Uponor TruFLOW manifold installed in the condominium building.
The radiant system design called for a number of Uponor products, including: 15,500 feet of 1/2-inch Wirsbo hePex plus tubing; 14 TruFLOW manifolds; three proMIX 101 mixing controls with motorized three-way valves to control supply water temperature; 3,000 feet of 3/4-inch Wirsbo hePex plus tubing for the snow-melt system; 2-inch copper manifolds with integral isolation and loop balance valves; 5/8-inch and 3/4-inch multilayer composite tubing (PEX-AL-PEX) to connect the remote manifolds to the boiler room (the supply/return mains were insulated to prevent heat loss); and thermal actuators.
During the rehab, Foley Mechanical also installed: two Lochinvar Knight KBN-500 500,000 Btuh condensing gas boilers with thermal efficiencies above 90 percent; Carrier HVAC rooftop units; Aaon make-up air ventilation equipment; Penn exhaust fans; two Heat Transfer Products Super-Stor commercial indirect water heaters; tekmar staging and snow-melt controls; a Flat-Plate heat exchanger for the snow-melt system; Grundfos pumps; a Caleffi Hydro-Separator; Taco relays and controls; Aprilaire communicating network thermostats; Nortec steam humidifiers; Honeywell air cleaners; Ruskin louvers; and two Penn 7500-cfm garage exhaust fans.
Some of this equipment was installed because the engineer specified a forced-air system. The engineer wanted a backup system because of the ceiling height in the living spaces.
“We designed and installed a totally redundant system where we have hot decks in every air handler,” Foley says. “Either system can carry 100 percent of the heating load.
“To our way of thinking, the dual-heating plan offers residents a two-stage system with the radiant floor heat as the primary. If the temperature in the space drops three degrees from the set temperature, the fan coil comes on and blows hot air into the room.”

Foley Mechanical had two days with a 12-man crew to lay 15,000 feet of PEX tubing.
Installation Overdrive
Confined spaces made for confined working conditions and even tighter work schedules. Encore Development couldn’t afford to shut down the site for a week while Foley’s customary three- or four-man crew laid all the PEX tubing for the radiant heating. So, Foley increased the number of crew members to 12 and reduced the number of days to a Friday and Saturday.“We were rocking and rolling, trying not to trip over each other, to get all the tubing down in only two days,” he says. “It worked.”
To ensure that all the tubing was installed according to plan - despite the speed - Foley’s team used spray paint to detail the tubing layout. The floor consists of a structural steel deck, 4-inch concrete layer, 2-inch extruded polystyrene and 4-inch capping slab that houses the radiant tubing.
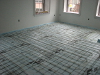
The floor consists of a structural steel deck, 4-inch concrete layer, 2-inch extruded polystyrene and 4-inch capping slab that houses the radiant tubing.
Summit worried, however, that the tubing penetrations through the slab might undermine its structural integrity.
“After setting the corrugated steel deck, we sleeved all of our penetrations,” Foley says. “Then we put down 2 inches of foam and the 4-inch capping slab. This solution cost Encore a bit extra, but Summit’s concerns were met. Fortunately, the 14-foot ceilings meant we had the space to do it.”

The Wormley condos are designed with a dual-heating plan - radiant floor heat as the primary system with a forced-air system for backup - because of the 9- to 14-foot-high ceilings.
Lower Installation Cost
To lay 15,000 feet of PEX tubing in two days took more than precise scheduling and a clear picture of the pipe layout.“The physical toll on the hands of my crew would have been major with that much tubing installed in so small a time frame,” Foley notes.
The solution was Max Tool’s tie tool, which originally was designed to tie rebar. The tool wraps the PEX, ties it off and cuts the wire in half a second. Foley first saw the tool in 2007 at ISH in Frankfurt, Germany. He found a U.S. distributor and purchased three for $2,300 each. He subsequently had them modified with an adjustable tension.
“The tools costs a lot, but my labor costs more,” he says. “These devices saved money for our clients in the form of reduced installation time. More importantly, they also saved wear and tear on my crews.
“They’re not expensive when you look at what I’m paying my guys. The tools make them more productive.”