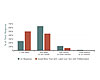
Table 1.
Long lead times may not impact business operations in the current context with a shortage of work. In the 2010 Contractor Prefabrication Survey conducted byFMI, 64 percent of respondents said their companies require a one-week to one-month lead time for prefabricated assemblies (Table 1). When the economy rebounds and building restarts, however, waiting a week or more for an assembly to arrive in the field could result in late completion dates and negative impacts to other trades.
In advance of an uptick in the economy, plumbing and mechanical firms can take advantage of a couple tools to reduce lead times and institute sustainable improvements: lean thinking and BIM.
Lean thinking is the elimination of waste and a pursuit of continuous improvement. We are familiar with how automobile companies embraced the “lean” concept to streamline their production plants and improve the flow of operations. In the last 20 years, the same concepts were adapted to eliminate excess costs and improve lead times throughout the automotive parts and distribution supply chains.
This special application was adapted and made famous by Dell and Walmart in the recent decade. These firms have learned how to reduce or nearly eliminate lead times from suppliers to ensure on-schedule delivery as a competitive advantage.
Surprisingly, 24 percent of contractors that responded to FMI’s prefabrication survey had never analyzed the efficiency of their prefabrication efforts (Table 2).
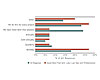
Table 2.
Mapping The Process
The best performing plumbing and mechanical contractors study their overall construction process and document it in a value-stream map. It is called “value stream” because the display of each step depicts product transformation, thus increasing value while moving through the process. Process mapping is the first step taken by contractors that apply lean thinking to improve their operation.The construction of steel piping systems offers a good case study. Refer to the value-stream map for a hypothetical plumbing and mechanical firm (Chart 1). According to this process, a designer first details the routing of the lines and placement of valves and other components. Then, a bill of materials is generated and purchasing expedites the order of piping and components. The prefabrication shop receives these materials and the drawing package and begins work on prepping, cutting, facing and welding the assembly. The assembly is bagged and tagged, then trucked to the field and installed in sequence.
That general sequence of steps seems plausible at the high level. But, there are details buried within these steps where unnecessary actions are taken, which cause the actual flow of value to be disjointed and uneven - resulting in waste. Some of this waste directly influences lead times. In this example, lead time is defined as the time between the recognition of the need for an assembly and the receipt of the assembly in the field:
Date Received in the Field – Date Requested by the PM = Lead Time (Days)
The project manager or superintendent recognizes through his weekly job-planning meetings what assemblies or spools are needed and when. These observations become weekly requests back to the head office. Lead time is measured in days and equals 26 days in the example process. Looking at the timeline at the bottom of the map, this process has 16 days of value-added activities (displayed on the bottom) and 10 days of nonvalue-added and value-enabling activities (displayed on the top). The operations manager can begin to discover methods to reduce the 10 days without disrupting the flow of the process.
Faced with this situation, a plumbing and mechanical contractor in the Southeast created a fishbone diagram, such as the one inChart 2, in order to uncover the reason for excessive lead times. The fishbone chart is comprised of the problem (steel construction lead time too long) on the right, with six main categories forming the “bones” of the fish. Likely causes were brainstormed with team members and added to the bones. Based on this assessment, the company quickly determined that its issues with lead time were not machine-, man-, measurement- or materials-related.
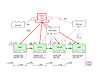
Chart 1.
Once the work package was issued to the prefabrication shop, the material began being transformed by the craftsmen according to the work package. However, in the middle of the flowing assembly shop, or “production” line, the whole process came to an abrupt stop as the welder had to study the drawings and determine where the field welds would have to go, then pick up a red pencil and mark up the work package. We might call this activity on the shop floor as “rework” or “processing” waste, because the craftsman had to correct or re-process the drawings that he received into a new format that was field-oriented in thinking.
Using value-stream mapping and fishbone diagrams, this firm reduced its average lead times from 26 days to 24 days - an 8 percent improvement. Work package creation and development included the details of weld information and specific field welds that are needed so that the assembly line can operate without stoppage. This also caused the individual work elements to become smaller - single piece - in nature, which resulted in even flow on the shop floor.
Mapping helps to visualize the flow of information, materials and value in any process and is specifically used to improve flow and timing of processes. Fishbone diagrams are useful for identifying root causes of problems.
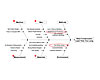
Chart 2.
Visualizing With BIM
The other tool that works in conjunction with lean thinking to reduce lead times is the use of building information modeling. BIM can be defined as the creation and coordinated use of a collection of digital information about a building project. The information can include cost, schedule, fabrication, maintenance, energy and 3D models.The information is used for design decision-making, production of high-quality construction documents, predicting performance, cost estimating, construction planning, and managing and operating the facility.
As shown in the value-stream map, steel piping lead times can be significantly influenced by the duration of the design effort. BIM dramatically reduces the time for detailed design through clash detection and visualization of the sequence of field work.
With all of the benefits of a single coordinated model, the broad application of this technology is quietly vexed by the issue around who should own the model. This question is rooted in the issue of ownership and risk. One argument is that the engineer-of-record should be responsible for the model since that entity is responsible for the design. However, as we’ve shown, the plumbing and mechanical contractor has to manage the flow of materials, information and resources through the construction value stream.
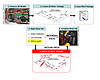
Chart 3.
Nonetheless, plumbing and mechanical firms with best-in-class performance implement BIM to demonstrate detailed design in a simulated environment, visualize the flow of construction, enhance sharing of information and efficiently coordinate resources. According to the prefabrication study, BIM is expected to play an important role in the growth and efficiency of prefabrication.
Plumbing and mechanical contractors can apply lean thinking and BIM to reduce lead times for prefabricated assemblies being shipped to the field. The first step in this process is to look holistically at all aspects of the business - from the point the project is sold to the point in which the project is closed out in the field.
Value-stream mapping is a way to visualize the flow of information, material and resources, while fishbonediagrams help to uncover root causes. BIM usage by plumbing and mechanical contractors is on the rise in order to improve the quality of output and certainty of success in the field.