Newest Joining Method For Any Piping System
Introducing the structural adhesive joining system.
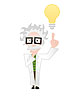
I received a call from my good friend Tommy Jamison of Mueller Industries regarding a new joining system. It was veiled in secrecy, but he wanted to know my opinion.
Let me give you some background information. I have known Tommy for many years. He is one of the most brilliant engineers in the copper tube and fitting business. He is well-respected in the industry. When he has a new application in for a patent, watch out.
Tommy explained to me that Mueller invented solder joints for copper tube more than 75 years ago. That was something I didn’t know. I often wondered who first came up with soldering. It was quite an invention, especially more than 75 years ago.
The new joint that Tommy was working on was a structural adhesive joint. My first thought was a two-part epoxy. I asked, “Hasn’t that been done already? Can’t you still buy some of these epoxies at Home Depot?”
Tommy’s response was, “Haven’t you noticed that none of them work?”
Not only me, but just about everyone in the plumbing profession knows that the epoxies are not a good means of joining copper tube. Even if the pipe and fitting stay together, the joint leaks. We have all seen joints with mounds of epoxy encapsulating the joint. All done in an effort to get it to stop leaking.
That’s when Tommy said that he figured out how to make the joint and prevent leaks.
By the time Tommy called me, Mueller had already completed a number of years of top-secret research on such a joining system.
There were two key factors required to make the joint: a means of sealing the joint and the use of true structural adhesives designed for the piping material, not your average everyday, two-part epoxy. Mueller knew that they were not in the structural adhesive business, so they called the experts - 3M.
If you have ever had to deal with 3M, you know that they have a bunch of Ph.D.s working behind closed doors somewhere in Minnesota inventing all sorts of great products. One such product is a structural adhesive to join sections of jet aircraft. That’s right; the next time you fly a new jet, look out the window and see how the sections of the plane are connected. In other words, this is some pretty good glue.
The structural adhesive was applied to the joint with a small handheld gun. The two tubes of the structural adhesive were connected, making it impossible to insert the adhesive incorrectly. The tip of the gun mixes the two parts a couple a thousand times. You get the idea.
When you apply the epoxy to the outside of the tube, you simply push it together. As I sat watching my first joint being made, I asked, “What if you make a mistake?” With that, the joint was pulled apart and the adhesive was wiped off with a rag. I was impressed.
That is when I asked for the details. How long before you can’t do that? When does the joint become strong? When can you pressure test? What are the limitations of the adhesive? So many questions, but complete intrigue.
As it turns out, they can make all types of structural adhesives. However, Mueller and 3M agreed to start with two - one that has a three-minute working life, also called the fast adhesive, and a 20-minute working life adhesive. It is anticipated that most installations will use the 20-minute adhe-sive. The three-minute adhesive is intended to be used for repairs.
I had the opportunity to witness a test of the fast adhesive on a joint after approximately 20 minutes. I could not believe the strength of the joints. Then I witnessed tests of fully cured joints.
On the slower adhesive, the cure time is approximately 24 hours. When they tried to pull the tube out of the fitting, the fitting fractured. You could not separate the structural adhesive joint.
The other testing that was done included a water hammer test, a vibration test and a thermocycling test. When the water hammer test is going, the entire laboratory shakes with each shock wave. The various tests are intended to simulate the worst-case condition you could possibly encounter in the field. The structural adhesive joining system came through all of the tests with flying col-ors.
The problem with seeing this demonstration and witnessing the testing was that I had to put it under my hat. I couldn’t say a thing to anyone. Every month, I would ask, “When can I write about it?” As you can see, I finally received permission to write about this new joining method.
Check it out and remember: It is not glue, it is structural adhesive.
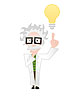
I received a call from my good friend Tommy Jamison of Mueller Industries regarding a new joining system. It was veiled in secrecy, but he wanted to know my opinion.
Let me give you some background information. I have known Tommy for many years. He is one of the most brilliant engineers in the copper tube and fitting business. He is well-respected in the industry. When he has a new application in for a patent, watch out.
Tommy explained to me that Mueller invented solder joints for copper tube more than 75 years ago. That was something I didn’t know. I often wondered who first came up with soldering. It was quite an invention, especially more than 75 years ago.
Brand New
Being a realist, Tommy knew that other joining methods for copper tube were being introduced and gaining a foothold in the industry. Mind you, Tommy, Mueller Industries and just about everyone in the copper business expect soldered joints to be around for many years to come. However, new joining methods have made amazing inroads in a few short years, including press-connect and push-fit fittings.The new joint that Tommy was working on was a structural adhesive joint. My first thought was a two-part epoxy. I asked, “Hasn’t that been done already? Can’t you still buy some of these epoxies at Home Depot?”
Tommy’s response was, “Haven’t you noticed that none of them work?”
Not only me, but just about everyone in the plumbing profession knows that the epoxies are not a good means of joining copper tube. Even if the pipe and fitting stay together, the joint leaks. We have all seen joints with mounds of epoxy encapsulating the joint. All done in an effort to get it to stop leaking.
That’s when Tommy said that he figured out how to make the joint and prevent leaks.
By the time Tommy called me, Mueller had already completed a number of years of top-secret research on such a joining system.
There were two key factors required to make the joint: a means of sealing the joint and the use of true structural adhesives designed for the piping material, not your average everyday, two-part epoxy. Mueller knew that they were not in the structural adhesive business, so they called the experts - 3M.
If you have ever had to deal with 3M, you know that they have a bunch of Ph.D.s working behind closed doors somewhere in Minnesota inventing all sorts of great products. One such product is a structural adhesive to join sections of jet aircraft. That’s right; the next time you fly a new jet, look out the window and see how the sections of the plane are connected. In other words, this is some pretty good glue.
Seeing Is Believing
When I first saw the fitting, it looked like a press-connect fitting. There was a hump in the copper fitting. Looking on the inside, there appeared to be an o-ring. However, that is where I was wrong. What appeared to be an o-ring was actually a split gasket. A lightbulb went off in my brain. Of course! A split gasket is much more secure in making a joint than an o-ring since there are multiple points of contact, not just one like on an o-ring.The structural adhesive was applied to the joint with a small handheld gun. The two tubes of the structural adhesive were connected, making it impossible to insert the adhesive incorrectly. The tip of the gun mixes the two parts a couple a thousand times. You get the idea.
When you apply the epoxy to the outside of the tube, you simply push it together. As I sat watching my first joint being made, I asked, “What if you make a mistake?” With that, the joint was pulled apart and the adhesive was wiped off with a rag. I was impressed.
That is when I asked for the details. How long before you can’t do that? When does the joint become strong? When can you pressure test? What are the limitations of the adhesive? So many questions, but complete intrigue.
As it turns out, they can make all types of structural adhesives. However, Mueller and 3M agreed to start with two - one that has a three-minute working life, also called the fast adhesive, and a 20-minute working life adhesive. It is anticipated that most installations will use the 20-minute adhe-sive. The three-minute adhesive is intended to be used for repairs.
I had the opportunity to witness a test of the fast adhesive on a joint after approximately 20 minutes. I could not believe the strength of the joints. Then I witnessed tests of fully cured joints.
On the slower adhesive, the cure time is approximately 24 hours. When they tried to pull the tube out of the fitting, the fitting fractured. You could not separate the structural adhesive joint.
The other testing that was done included a water hammer test, a vibration test and a thermocycling test. When the water hammer test is going, the entire laboratory shakes with each shock wave. The various tests are intended to simulate the worst-case condition you could possibly encounter in the field. The structural adhesive joining system came through all of the tests with flying col-ors.
The problem with seeing this demonstration and witnessing the testing was that I had to put it under my hat. I couldn’t say a thing to anyone. Every month, I would ask, “When can I write about it?” As you can see, I finally received permission to write about this new joining method.
Check it out and remember: It is not glue, it is structural adhesive.
Links
Looking for a reprint of this article?
From high-res PDFs to custom plaques, order your copy today!