Ticked Off, Part 1
Reducing noise from heat transfer plates within
radiant panels.
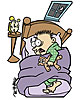
Imagine your family just moved into a new home with radiant floor heating. During your first night, the heating system turns on at 3 a.m. You don’t hear a thing because you’re sound asleep. However, within a few minutes, the floors in several rooms start emitting “ticking” sounds. These sounds repeat themselves and come from different areas of the floor.
Eventually they get sufficiently frequent and loud enough to wake one of your young children. Having no idea what’s causing the sound, your child panics, thinking someone is trying to hack their way into the bedroom. Terrified, the child runs from the room and jumps into bed with you. After some investigation, you determine the sound is coming from the floor heating system, which consists of PEX tubing and aluminum heat transfer plates.
Early the next morning, while you’re still “ticked off” over the situation, you debate whether the first call should be to your real estate agent or your attorney.
How would you like to be the heating contractor responsible for the above installation?
I didn’t think so…
So how can you, as a hydronic heating professional, steer clear of a similar situation?
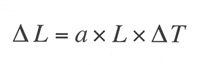
All materials expand when heated and contract when they cool. This certainly includes PEX tubing and aluminum heat transfer plates. The amount of expansion is determined by the initial length of the object, as well as a physical property of the material called its coefficient of linear expansion.
The change in length due to change in temperature can be calculated using Formula 1.
Where:
∆L = change in length due to temperature change (inch)
a = coefficient of linear expansion (inch/inch/degrees F)
L = original length (inch)
∆T = temperature change (degrees F)
The coefficients of linear expansion for most materials are very small numbers. Figure 1 gives some values for these coefficients relevant to the situation being discussed:
Here’s how Formula 1 can be used along with the data
in Figure 1.
Assume a straight run of copper tubing that’s exactly 50 feet long when at an initial temperature of 65 degrees F. The tube is wrapped in insulation. How much does the tube’s length change when it’s filled with 200-degree F water?
We’ll assume the insulated copper tube is very close to 200 degrees F when filled with water at this temperature. The coefficient of linear expansion for copper is 0.0000094 inch/inch/degrees F. Putting the numbers into Formula 1 yields:
Hence, the copper tube increased in length by a little over 3/4 inches. That’s a significant change in length, especially if the tube is rigidly clamped at its ends, or connected to elbows that pass through holes in the floor. In the latter case, those holes need to have a diameter that allows for the tube’s expansion without letting it press against the side of holes. If this is not the case, the tube will be stressed, possibly to the point of buckling.
It’s important to understand that a solid material does not emit any sound of its own while expanding or contracting, provided the movement is not impeded by surrounding materials or supports. It’s also important to realize that the atomic level forces that cause thermal expansion are extremely powerful. They cannot be “overpowered” by stronger fasteners or surrounding materials. Instead, sufficient space must be provided to accommodate the expansion movement. Not doing so can lead to high compressive stresses within the materials.

The change in length of the aluminum plate is:
The change in length of the PEX tube is:
Although both numbers appear small, the difference between them is what counts. In this case, the PEX tubing expands about 0.146 inches more than the aluminum plate surrounding it. This differential expansion is part of what causes the ticking sounds.
Another contributor is a phenomenon called “stiction,” which occurs between the external EVOH oxygen diffusion barrier coatings on some PEX tubes and the aluminum plates. Stiction is a situation in which the outer surface of the tube weakly bonds to the aluminum plate. This allows compressive stress to build within the tube wall as it warms up. At some point, the accumulating compressive stress in the tube wall reaches the point where it breaks the loose bond with the plate. The tube instantly moves a small amount along the plate; a “tick” is the result.
This effect is enhanced by rapid temperature changes that occur when hot water from the boiler races down a tube that’s been at room temperature for some time. As if this weren’t enough, some ticking noise might be the result of differential expansion between other materials in the floor including plywood, rigid insulation or quasi-rigid floor coverings such as wood and tile. All these materials have different coefficients of linear expansion and, thus, are subject to differential expansion as the system transitions from one quasi-steady state temperature to another.
So what can be done about reducing ticking sounds? Fortunately, there are several tactics that, when used collectively, will virtually guarantee you won’t build a radiant panel that sounds like a commercial for Rice Krispies. Some deal with material choices, while others rely on specific installation details. Next month we’ll look at ways to put them all together to deliver silent comfort from plate-based radiant panel systems.
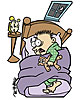
Imagine your family just moved into a new home with radiant floor heating. During your first night, the heating system turns on at 3 a.m. You don’t hear a thing because you’re sound asleep. However, within a few minutes, the floors in several rooms start emitting “ticking” sounds. These sounds repeat themselves and come from different areas of the floor.
Eventually they get sufficiently frequent and loud enough to wake one of your young children. Having no idea what’s causing the sound, your child panics, thinking someone is trying to hack their way into the bedroom. Terrified, the child runs from the room and jumps into bed with you. After some investigation, you determine the sound is coming from the floor heating system, which consists of PEX tubing and aluminum heat transfer plates.
Early the next morning, while you’re still “ticked off” over the situation, you debate whether the first call should be to your real estate agent or your attorney.
How would you like to be the heating contractor responsible for the above installation?
I didn’t think so…
So how can you, as a hydronic heating professional, steer clear of a similar situation?
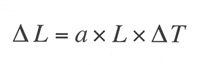
Formula 1
Guaranteed Growth
The first step to avoiding it is understanding why the noises are generated. They are caused by rapid temperature changes in combination with materials having significantly different physical characteristics.All materials expand when heated and contract when they cool. This certainly includes PEX tubing and aluminum heat transfer plates. The amount of expansion is determined by the initial length of the object, as well as a physical property of the material called its coefficient of linear expansion.
The change in length due to change in temperature can be calculated using Formula 1.
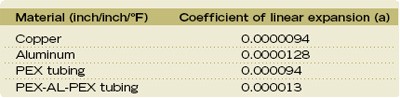
Figure 1
∆L = change in length due to temperature change (inch)
a = coefficient of linear expansion (inch/inch/degrees F)
L = original length (inch)
∆T = temperature change (degrees F)
The coefficients of linear expansion for most materials are very small numbers. Figure 1 gives some values for these coefficients relevant to the situation being discussed:

Assume a straight run of copper tubing that’s exactly 50 feet long when at an initial temperature of 65 degrees F. The tube is wrapped in insulation. How much does the tube’s length change when it’s filled with 200-degree F water?
We’ll assume the insulated copper tube is very close to 200 degrees F when filled with water at this temperature. The coefficient of linear expansion for copper is 0.0000094 inch/inch/degrees F. Putting the numbers into Formula 1 yields:
Hence, the copper tube increased in length by a little over 3/4 inches. That’s a significant change in length, especially if the tube is rigidly clamped at its ends, or connected to elbows that pass through holes in the floor. In the latter case, those holes need to have a diameter that allows for the tube’s expansion without letting it press against the side of holes. If this is not the case, the tube will be stressed, possibly to the point of buckling.
It’s important to understand that a solid material does not emit any sound of its own while expanding or contracting, provided the movement is not impeded by surrounding materials or supports. It’s also important to realize that the atomic level forces that cause thermal expansion are extremely powerful. They cannot be “overpowered” by stronger fasteners or surrounding materials. Instead, sufficient space must be provided to accommodate the expansion movement. Not doing so can lead to high compressive stresses within the materials.

Different Strokes
Next, let’s compare the difference in expansion between a segment of PEX tubing and an aluminum heat transfer plate, both of which are 24 inches long at 65 degrees F, and both of which rise to 140 degrees F when operating in a radiant panel system.The change in length of the aluminum plate is:

Although both numbers appear small, the difference between them is what counts. In this case, the PEX tubing expands about 0.146 inches more than the aluminum plate surrounding it. This differential expansion is part of what causes the ticking sounds.
Another contributor is a phenomenon called “stiction,” which occurs between the external EVOH oxygen diffusion barrier coatings on some PEX tubes and the aluminum plates. Stiction is a situation in which the outer surface of the tube weakly bonds to the aluminum plate. This allows compressive stress to build within the tube wall as it warms up. At some point, the accumulating compressive stress in the tube wall reaches the point where it breaks the loose bond with the plate. The tube instantly moves a small amount along the plate; a “tick” is the result.
This effect is enhanced by rapid temperature changes that occur when hot water from the boiler races down a tube that’s been at room temperature for some time. As if this weren’t enough, some ticking noise might be the result of differential expansion between other materials in the floor including plywood, rigid insulation or quasi-rigid floor coverings such as wood and tile. All these materials have different coefficients of linear expansion and, thus, are subject to differential expansion as the system transitions from one quasi-steady state temperature to another.
So what can be done about reducing ticking sounds? Fortunately, there are several tactics that, when used collectively, will virtually guarantee you won’t build a radiant panel that sounds like a commercial for Rice Krispies. Some deal with material choices, while others rely on specific installation details. Next month we’ll look at ways to put them all together to deliver silent comfort from plate-based radiant panel systems.
Links
Looking for a reprint of this article?
From high-res PDFs to custom plaques, order your copy today!