
Over this time, the controls industry has responded to the demand for such systems by developing a variety of dedicated purpose controllers, such as outdoor reset controls, boiler staging controls, zoning coordination and mixing controls.
It is not at all uncommon to see several of these controllers combined in a single system. Since these controls each require power, sensor wiring, as well as interconnection to the other controls, a typical arrangement mounts each “box” adjacent to a wiring gutter. An example of such a system being installed is shown in Figure 1.
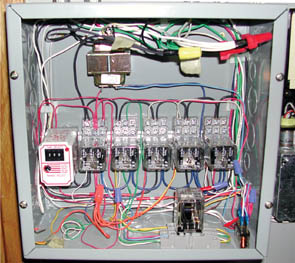
Copper Fettuccini
Those who have installed “multiple box” control systems, such as shown in Figure 1, can vouch for the fact that they take a considerable amount of planning and installation time. They also require careful adjustment to avoid the possibility of conflicting control logic. The latter becomes even more probable when the driven devices also contain “smarts,” especially when they come from a variety of different manufacturers.In addition to dedicated purpose controllers, the operating logic of some systems also requires some general-purpose relays. They may be used to complete the required overall system logic, especially in designs that stray from the functionality provided by dedicated controllers.
By wiring the relays together in various combinations of series and parallel, one can create “hard-wired logic.” Although such wiring can work well for many years, it will eventually have to be serviced or modified. If it looks anything like the wiring shown in Figure 2, this could be a challenge.
Unless such wiring is accompanied by a corresponding ladder diagram, anyone attempting to service it will likely spend considerable time trying to trace down the various circuits and recreate the operating logic conceived by the original installer. This is not an approach that builds confidence in the minds of customers.
Although the multiple box approach has served the needs of the industry well as the demand for more specialized systems has grown, it’s not the end of the road as far as control technology is concerned.

Multiple Personalities
There is a definite change afoot for future hydronic control products. Instead of coming to market with a wide variety of dedicated controllers, manufacturers will rely more and more on programmable control devices.A given “box” will be able to perform a variety of tasks based on the software it is operating at the time. A good analogy would be a PC. With the right software, the same computer can serve the needs of a CPA, an engineer or even a die-hard gamer.
Imagine being able to select a “template” for a given system from a library of say 1,000 possible system configurations. One part of that template would be a piping schematic that shows exactly how the system should be piped.
Every circulator, valve, boiler and so on would have a unique designation. For one job you may need a system that operates two boiler stages, provides priority operation of an indirect water heater, and simultaneously supplies three different water temperatures to various space heating loads.
No problem. You’ll likely follow a menu tree on you PC monitor that guides you to the requisite configuration. Maybe this time it’s system configuration No. 514.
Another aspect of the template will be the software instructions for the programmable controller. Once the system configuration is selected, these instructions may be quickly downloaded to the controller from your laptop computer or PDA (personal digital assistant).
Alternately, the software may be linked to the controller by inserting a small memory device resembling a credit card as shown in Figure 3. Slip in one card and the controller can operate a four-stage boiler system. Slip in another and the same controller can manage two or three mixing devices, as well as an indirect water heater. You get the idea.
Most of the initial settings required by the system would already be made. Over time, the controller will likely have the ability to automatically alter these initial settings as it “learns” how the system responds, and seeks to optimize performance.
Still another component of the template would be a “pin out” diagram of the terminals on the controller showing exactly how each external device should be wired to it. In one application, terminals 3 and 4 might be connected to a temperature sensor. On the next job, these same terminals might provide a low-voltage output to a modulating valve or variable speed circulator.
Laptop Vs. Pickup
Anyone who’s lived through the evolution in HVAC controls over the last 20 years can probably describe a situation in which they’ve driven 50-plus miles just to turn a couple of dials on a controller. Maybe that initial reset ratio was a bit too low, or the differential on the boiler staging control was a little too high. Perhaps on the way home the technician wondered if there would ever come a day when such an adjustment could be made without the road time.Turns out that day is here. Multifunction programmable controllers capable of being adjusted via the Internet already are on the U.S. market, and many more are sure to follow.
With these controls, you’ll be able to check out your system’s status directly from a Web page configured specifically for that system. Perhaps you’ll want to examine the operating history of the system over the last several days.
Based on this you might want to make an adjustment or two to the settings. You might even instruct the controller to send you automatic e-mails if certain control parameters reach designated values. This kind of access will save you considerable time and aggravation.
For several years I’ve been convinced that advancements in control technology will be mind boggling compared to what the industry used only 25 years ago. The products that are now appearing on the market have certainly bolstered that belief.
Can you remember life before fax machines? How about before e-mail? Although there was some learning before you reaped the benefits of this new technology, it soon became the norm. There’s little question both improved your ability to communicate more efficiently, which directly improved your bottom line.
Similarly, those who want to take advantage of all modern hydronic heating has to offer must take the time to learn about these new control methods and hardware.
Stay tuned. Later this year we’ll get into even more depth on the benefits to be served up by modern control technology.