To Condense Or Not To Condense
Carol Fey
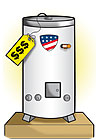
What’s all this debate about condensing vs. noncondensing boilers? It seems to be like so many topics - religious, political - that everyone has an opinion and just knows he’s right. Why is he right? Well, because he is, that’s why.
I like to find reasons that are more data-based. But first, I must point out two things. One is that the reason to consider using a more expensive condensing boiler is expected increased efficiency. The second thing I want to mention is that some of the additional efficiency depends upon the controls, especially outdoor reset. I’ll deal with that in an upcoming column. But for now, let’s talk about whether to condense or not to condense.
Whenever there’s combustion (which, after all, is what a boiler is for), there is condensation. The important factor is where the condensation happens.
When we have combustion in a boiler, we always have flue gases. Flue gases cool, and when they cool, the water vapor in the flue gases normally condense into water. When there’s condensation, heat is released and - here’s the important part - the heat that’s released is free!
Traditionally, we let the free heat go up the flue. But if the conditions are right, we can capture that heat and keep it in the boiler heat exchanger. On the other hand, condensation does not always occur. If the flue gas temperatures are high enough as it leaves the stack, and the atmosphere has a low humidity and high enough temperature, the moisture in the flue gases will not condense.
If we, however, add that free heat to the system, we can call it increased efficiency.
So that gets us to Principle No. 1: Condensing flue gases in the heat exchanger increases boiler efficiency. And that immediately takes us to Principle No. 2: Condensing flue gases somewhere other than the heat exchanger, such as in the flue, lets the heat escape and does not increase efficiency.
In other words, if your customer pays you more money for a condensing boiler and you let the flue gases condense in the flue, you have wasted your customer’s money.
However, we also have to contend with Principle No. 3: If you let flue gases condense in the heat exchanger of a noncondensing boiler, you damage the boiler or the flue. This also wastes your customer’s money.
Power To Decide
Maybe you didn’t know that you have the power to decide where flue gases condense. Maybe you haven’t even thought about flue gases much, other than to hope they just safely go away. I’ll bet you thought - as I did - that the technology of the boiler determines whether there’s condensing, and that there wasn’t an issue.Here’s an example of just that.
Jeff installs a condensing boiler. He knows that condensing means that liquid - a fairly high-acid water (approximately 4.5 pH) - comes out as a product of the efficient combustion. He sees a small amount of water coming out of the boiler, so he takes that as proof that the high-efficiency boiler is working. Sure, there’s condensation. The question is, where is the condensation happening? If it’s happening in the flue, there will be evidence of condensation, but the free heat goes up the flue. No improved efficiency!
It turns out that condensation is going to begin to happen wherever the flue gases drop to about 130 degrees F. If you have a condensing boiler and you want to get full efficiency, you need to get the temperature to be about 60 degrees F or less in the heat exchanger. If you have a noncondensing boiler, you need to be sure that the flue gases don’t get that cool.
Noncondensing boilers use vent materials that will not last if the flue gases condense in the vent. So you don’t want the flue gases to condense even in the stack of a noncondensing boiler.
The idea is simple enough. The question is, how do you control that? This turns out to be simple, too. The temperature of the return boiler water can control the temperature of the gases. Cooler return water makes for cooler flue gases in the heat exchanger.
But wait a minute! Wait a minute on two things! First, when you set the aquastat, you’re controlling the temperature of the water leaving the boiler, not the temperature returning. So how are you going to control the return temperature, if you don’t have a boiler that controls return water temperature?
Second, there are 100-year-old guidelines that say water temperature should be a lot higher than 130 degrees F for the classic applications:
That takes care of the water leaving the boiler. The rule for return water is that it should be 20 degrees cooler than when it left the boiler. So we knock 20 degrees off any of the temperatures listed above, and we’re still well above 130 degrees F.
It gets worse. We can figure that the flue gases leaving the heat exchanger are about 7 degrees hotter than the return water temperature. So if the return water is 140 degrees F, the flue gases are 147 degrees F.
This is somewhat determined by the boiler’s design, water flue rate and firing rate. You can have flue gas temperatures as much as 140 degrees F to 150 degrees F higher than return water temperatures in some boilers.
We can argue at length about whether you could or should lower the supply water temperature. But take a moment to think about where the recommended water temperatures came from. They’re from about 100 years ago when central heating first became the rage. Buildings were different then. They were leaky. They weren’t insulated. Windows were single-pane. R-values hadn’t been invented yet!
Also think about this. The assumption behind those recommended water temperatures is that the outside temperature is somewhere around zero, varying from north to south. That means that your boiler is ready to deal with low temperatures all day, every day. The other temperature assumption is that you are going to heat the inside to 72 degrees F. Depending upon the situation, this, too, may not be realistic.
Besides lowering the temperature of the water leaving the boiler, another way to reduce return water temperature is to increase the difference (∆T) between the supply and return water. We won’t go into that here, but, of course, there are ways that can be done.
Regardless, for this conversation about condensing boilers, here’s what it comes down to. If you can’t decrease the return water temperature to the low 120s - enough to get the flue gases below 130 degrees F - you give up the increased efficiency of a condensing boiler. In a condensing boiler, if your flue gases remain above 130 degrees F, count on your efficiency percentage rating dropping from the mid-90s to the high-80s.
If you can’t justify reducing the return water temperature enough, you might be better off recommending a less expensive noncondensing boiler to your customer. But if you’re working with a condensing boiler, remember that whether it condenses or not - whether it’s highly efficient or not - is in your hands as the guy who determines the return water temperature.
Looking for a reprint of this article?
From high-res PDFs to custom plaques, order your copy today!