Mountaintop Experience
John Siegenthaler says, if there's ever been a time to get serious about slab insulation, it's now!

A wide variety of opinions on what constitutes proper underslab insulation continue to exist in the North American radiant panel industry. They range from “No underslab insulation is needed because everyone knows heat rises,” to “Is 4 inches of extruded polystyrene enough insulation under my basement slab?”
Where do you fall within this spectrum? Do you consider underslab insulation an inseparable component of any successful slab-on-grade radiant floor installation, or a waste of time and money?
A phone call I recently received from a very disappointed building owner could probably define the lower end of this spectrum. Here’s a quick summary of the situation he finds himself in.
Imagine a masonry block structure with a concrete floor slab built on solid rock at the top of a mountain. The floor slab is about 5 feet above the surrounding grade. The building has no insulation. It was formerly used and heated by the U.S. government using multimillion Btu/hr. furnaces installed in the 1950s.
The government no longer needed the facility, so it was sold for private use. The new owner planned to convert it to a shop, and heard that radiant floor heating would be an ideal match. He pursued this with a local installer, who told him there was no need for insulation under the new heated slab floor. It could just be poured over the existing floor.
About $50,000 later, the owner has a radiant floor heating system that, on a good day, can maintain the building somewhere in the low- to mid-50 degrees F range, assuming the boiler runs nonstop.
I’ve never seen this building, but from the description given me I find it almost unbelievable that such an installation really took place. The current lack of insulation on the building’s walls can be remedied, but the new heated slab will do little beyond adding a few inches to the floor elevation, and serve - in the most literal sense - as a source of global warming.
All those involved in the project now realize this approach was a big mistake. How it all gets sorted out is yet to be determined, but needless to say a tidy sum of money will be required before this building ever produces the comfort originally sought by its owner.

The mere possibility of such price escalation should profoundly influence decisions that impact building energy use for decades to come. How foolish is it to claim we install “green” heating systems that use high-efficiency boilers, geothermal heat pumps or other equipment, only to let that heat leak out from under our buildings at rates reminiscent of the 1950s? Energy codes are supposed to avert these situations but, as always, some projects manage to sidestep codes, and that’s where the professionalism of those working on the structure and its mechanical systems can, with any luck, save the owner from himself.
Although we profit by installing efficient hydronic heating systems, doing so in energy-inefficient buildings is never in the best interest of the customer. It’s also likely to lead to eventual complaints from owners who thought their new high-tech heating systems would miraculously cure the energy appetite of their buildings.
Ten To One: I like to raise the following question during discussions on underslab insulation: “If the initial method used to insulate the slab eventually proves insufficient, how hard is it to retrofit proper underslab insulation?” This question always produces some laughs, but for some the chuckles quickly fade to sobering realizations as specific projects come to mind. Projects where little, if any, underslab insulation was used.
Of course, it is possible to retrofit underslab insulation, but the required building disruption, cost and mess make it extremely unlikely. Hence, the initial methods and materials used for underslab insulation are all but certain to remain in place for the life of the structure, whether they work or not.
I believe that downward heat loss from a heated floor should not exceed 10 percent of upward heat output. This ratio comes from a European (DIN) installation standard for floor heating systems, a standard that was established long before the current energy cost situation.
The R-value of underslab insulation that allows this 10:1 ratio to be attained is affected by factors such as floor coverings, required upward heat flux and soil temperature. Here’s a summary of the basic physics and a way to calculate the minimum required R-value.
Think of the floor slab as a heated plane sandwiched between the finish floor material(s) on top and underside insulation below as shown in Figure 1.
The
resistor symbols shown on the right represent the R-values of the various
materials and air-films. The upward and downward heat flow rates are determined
by these resistances, as well as by the temperature of the slab plane relative
to room air temperature and soil temperature.
Formula 1 can be used to determine the minimum R-value of the underside insulation so that downward heat loss is no more than 10 percent of upward heat delivery.
Formula 1
Where:
Rui = minimum R-value of underside insulation (degrees F•hr•ft2/Btu)
Tsoil = soil temperature below slab at design load conditions (degrees F)
Troom = room air temperature at design load conditions
Rff = total R-value of all finish flooring layers (degrees F•hr•ft2/Btu)
0.5 = approximate R-value of air film above floor surface (degrees F•hr•ft2/Btu)
qup = upward heat flux from floor at design load conditions (Btu/hr/ft2)
Here’s an example: Assume a room is maintained at 70 degrees F under design load conditions by a heated floor slab releasing 28 Btu/hr/ft2. The soil temperature under the slab insulation is estimated at 65 degrees F. The slab is covered with a floor covering having an R-value of 0.9 degrees F•hr•ft2/Btu. Determine the minimum R-value of the underside insulation based on the 10:1 assumption described above.
Solution: Putting the numbers into Formula 1 yields the required minimum R-value for the underside insulation:
A
3-inch thick layer of extruded polystyrene will produce an R-value of 16.2;
thus, it would be a good option in this situation.
Here’s another example: Assume a bare slab maintains a room at 70 degrees F with an upward heat flux of 20 Btu/hr/ft2. The soil temperature is again estimated at 65 degrees F. What’s the minimum underside R-value based on the 10:1 assumption?
Here are the numbers in Formula 1:
A 1 1/2-inch layer of extruded polystyrene would do the job in this application.
The calculated R-value for underside insulation goes up as the floor covering R-value goes up. The greater the resistance of the upward heat flow path, the greater the “motivation” for heat to be driven downward into the soil; thus, the higher the underside R-value needs to be.
In my area, the cost difference between 1-inch- and 2-inch-thick extruded polystyrene insulation board is currently about 48 cents per square foot. Using 2-inch rather than 1-inch extruded polystyrene would add about $720 to the cost of insulating under a 1,500-square-foot slab.
If the seasonable average slab temperature was assumed to hold about 10 degrees F above the seasonal average soil temperature, and this condition was sustained over a heating season lasting from October 1 through April 30, the heat loss associated with using 2-inch rather than 1-inch underslab insulation would be about 7.1 million Btus less. Although the rates of downward heat loss from the slab only differ by about 0.93 Btu/hr/ft2, this difference is present 24/7, and really adds up over the entire heating season.
Assuming heat was supplied from fuel oil purchased at $3.75 per gallon (about 45 cents/gallon less than I was quoted in mid-May) and burned in a boiler with an AFUE of 85 percent, the savings associated with the thicker insulation would be $224/year. That makes the simple payback on the 2-inch underslab insulation about 3.2 years! This far surpasses the economic returns associated with solar energy systems, wind turbines and other more “newsworthy” energy alternatives.
The mountaintop building described earlier is a relic of 1950s thinking. Upgrading it for service 50+ years later takes more than a new slab with embedded tubing. Professionals dealing with such renovations should carefully consider the cost implications of poorly insulated buildings over decades of future use. Given the current situation, such costs are likely to equal or exceed those associated with exterior maintenance, or even space reconfiguration, and should have commensurate weight in capital allocation decisions.
The energy price increases of the last year should make us all reexamine how we design and install systems. Systems that are, in large part, expected to operate over the life of the building. Minimizing loads beats overpowering them every time. Energy conservation is a win-win scenario, regardless of whether the prime motivator is carbon footprint or credit card balance.

A wide variety of opinions on what constitutes proper underslab insulation continue to exist in the North American radiant panel industry. They range from “No underslab insulation is needed because everyone knows heat rises,” to “Is 4 inches of extruded polystyrene enough insulation under my basement slab?”
Where do you fall within this spectrum? Do you consider underslab insulation an inseparable component of any successful slab-on-grade radiant floor installation, or a waste of time and money?
A phone call I recently received from a very disappointed building owner could probably define the lower end of this spectrum. Here’s a quick summary of the situation he finds himself in.
Imagine a masonry block structure with a concrete floor slab built on solid rock at the top of a mountain. The floor slab is about 5 feet above the surrounding grade. The building has no insulation. It was formerly used and heated by the U.S. government using multimillion Btu/hr. furnaces installed in the 1950s.
The government no longer needed the facility, so it was sold for private use. The new owner planned to convert it to a shop, and heard that radiant floor heating would be an ideal match. He pursued this with a local installer, who told him there was no need for insulation under the new heated slab floor. It could just be poured over the existing floor.
About $50,000 later, the owner has a radiant floor heating system that, on a good day, can maintain the building somewhere in the low- to mid-50 degrees F range, assuming the boiler runs nonstop.
I’ve never seen this building, but from the description given me I find it almost unbelievable that such an installation really took place. The current lack of insulation on the building’s walls can be remedied, but the new heated slab will do little beyond adding a few inches to the floor elevation, and serve - in the most literal sense - as a source of global warming.
All those involved in the project now realize this approach was a big mistake. How it all gets sorted out is yet to be determined, but needless to say a tidy sum of money will be required before this building ever produces the comfort originally sought by its owner.

Figure 1
One Chance To Do It Right
Three years ago, who would have predicted crude oil selling at $125 per barrel? Three years from now, who knows what the price of any fuel might be? As this column is being written, gasoline is selling for about $8.38/gallon in the United Kingdom, and in the United States the average is only $3.45/gallon. It appears there’s still ample room for continued price increases.The mere possibility of such price escalation should profoundly influence decisions that impact building energy use for decades to come. How foolish is it to claim we install “green” heating systems that use high-efficiency boilers, geothermal heat pumps or other equipment, only to let that heat leak out from under our buildings at rates reminiscent of the 1950s? Energy codes are supposed to avert these situations but, as always, some projects manage to sidestep codes, and that’s where the professionalism of those working on the structure and its mechanical systems can, with any luck, save the owner from himself.
Although we profit by installing efficient hydronic heating systems, doing so in energy-inefficient buildings is never in the best interest of the customer. It’s also likely to lead to eventual complaints from owners who thought their new high-tech heating systems would miraculously cure the energy appetite of their buildings.
Ten To One: I like to raise the following question during discussions on underslab insulation: “If the initial method used to insulate the slab eventually proves insufficient, how hard is it to retrofit proper underslab insulation?” This question always produces some laughs, but for some the chuckles quickly fade to sobering realizations as specific projects come to mind. Projects where little, if any, underslab insulation was used.
Of course, it is possible to retrofit underslab insulation, but the required building disruption, cost and mess make it extremely unlikely. Hence, the initial methods and materials used for underslab insulation are all but certain to remain in place for the life of the structure, whether they work or not.
I believe that downward heat loss from a heated floor should not exceed 10 percent of upward heat output. This ratio comes from a European (DIN) installation standard for floor heating systems, a standard that was established long before the current energy cost situation.
The R-value of underslab insulation that allows this 10:1 ratio to be attained is affected by factors such as floor coverings, required upward heat flux and soil temperature. Here’s a summary of the basic physics and a way to calculate the minimum required R-value.
Think of the floor slab as a heated plane sandwiched between the finish floor material(s) on top and underside insulation below as shown in Figure 1.
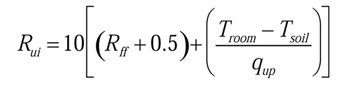
Formula 1 can be used to determine the minimum R-value of the underside insulation so that downward heat loss is no more than 10 percent of upward heat delivery.

Where:
Rui = minimum R-value of underside insulation (degrees F•hr•ft2/Btu)
Tsoil = soil temperature below slab at design load conditions (degrees F)
Troom = room air temperature at design load conditions
Rff = total R-value of all finish flooring layers (degrees F•hr•ft2/Btu)
0.5 = approximate R-value of air film above floor surface (degrees F•hr•ft2/Btu)
qup = upward heat flux from floor at design load conditions (Btu/hr/ft2)
Here’s an example: Assume a room is maintained at 70 degrees F under design load conditions by a heated floor slab releasing 28 Btu/hr/ft2. The soil temperature under the slab insulation is estimated at 65 degrees F. The slab is covered with a floor covering having an R-value of 0.9 degrees F•hr•ft2/Btu. Determine the minimum R-value of the underside insulation based on the 10:1 assumption described above.
Solution: Putting the numbers into Formula 1 yields the required minimum R-value for the underside insulation:

Here’s another example: Assume a bare slab maintains a room at 70 degrees F with an upward heat flux of 20 Btu/hr/ft2. The soil temperature is again estimated at 65 degrees F. What’s the minimum underside R-value based on the 10:1 assumption?
Here are the numbers in Formula 1:
A 1 1/2-inch layer of extruded polystyrene would do the job in this application.
The calculated R-value for underside insulation goes up as the floor covering R-value goes up. The greater the resistance of the upward heat flow path, the greater the “motivation” for heat to be driven downward into the soil; thus, the higher the underside R-value needs to be.
Justifiable Change
I’ve recently decided to specify a minimum of 2-inch extruded polystyrene (R = 10.8 degrees F•hr•ft2/Btu) insulation under all heated slabs, even those in basements with no floor coverings. This is a hedge against the possibility of future energy prices that will make $4 per gallon of gasoline look like a bargain. It’s also an economically justifiable choice as the following example illustrates.In my area, the cost difference between 1-inch- and 2-inch-thick extruded polystyrene insulation board is currently about 48 cents per square foot. Using 2-inch rather than 1-inch extruded polystyrene would add about $720 to the cost of insulating under a 1,500-square-foot slab.
If the seasonable average slab temperature was assumed to hold about 10 degrees F above the seasonal average soil temperature, and this condition was sustained over a heating season lasting from October 1 through April 30, the heat loss associated with using 2-inch rather than 1-inch underslab insulation would be about 7.1 million Btus less. Although the rates of downward heat loss from the slab only differ by about 0.93 Btu/hr/ft2, this difference is present 24/7, and really adds up over the entire heating season.
Assuming heat was supplied from fuel oil purchased at $3.75 per gallon (about 45 cents/gallon less than I was quoted in mid-May) and burned in a boiler with an AFUE of 85 percent, the savings associated with the thicker insulation would be $224/year. That makes the simple payback on the 2-inch underslab insulation about 3.2 years! This far surpasses the economic returns associated with solar energy systems, wind turbines and other more “newsworthy” energy alternatives.
The mountaintop building described earlier is a relic of 1950s thinking. Upgrading it for service 50+ years later takes more than a new slab with embedded tubing. Professionals dealing with such renovations should carefully consider the cost implications of poorly insulated buildings over decades of future use. Given the current situation, such costs are likely to equal or exceed those associated with exterior maintenance, or even space reconfiguration, and should have commensurate weight in capital allocation decisions.
The energy price increases of the last year should make us all reexamine how we design and install systems. Systems that are, in large part, expected to operate over the life of the building. Minimizing loads beats overpowering them every time. Energy conservation is a win-win scenario, regardless of whether the prime motivator is carbon footprint or credit card balance.
Links
Looking for a reprint of this article?
From high-res PDFs to custom plaques, order your copy today!